28. Jänner 2025
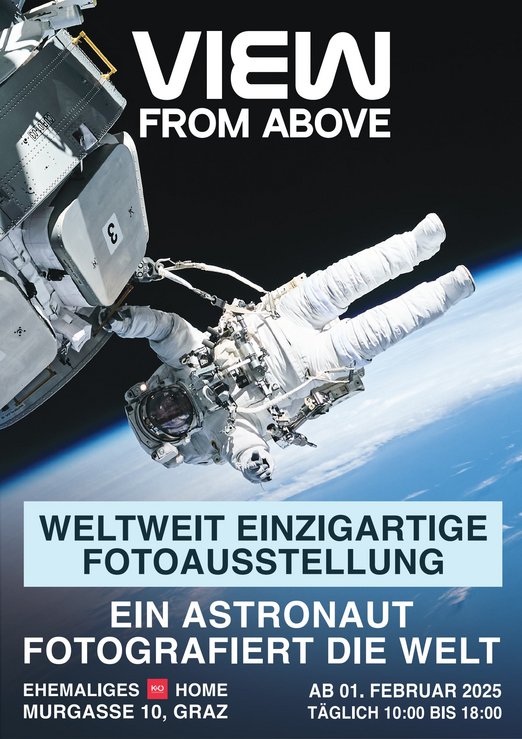
VIEW FROM ABOVE
Mit „View From Above“ kommt eine Weltpremiere in die Grazer Innenstadt. In der einzigartigen Ausstellung präsentiert NASA-Astronaut Terry Virts atemberaubende Fotografien, die während seiner Missionen auf der Internationalen Raum-station (ISS) entstanden sind. Vom 1. Februar bis 31. März 2025 können Besucher die Erde aus einer völlig neuen Perspektive erleben und tief in das Leben eines Astronauten eintau-chen – eine Premiere, die Wissenschaft, Kunst und Technologie vereint.
Die Erde, wie sie nur wenige gesehen haben
In der größten leerstehenden Geschäftsfläche der Innenstadt – dem ehemaligen „Home“-Gebäude von Kastner & Öhler – werden auf 1.500 m² rund 170 großformatige Fotografien und Videos präsentiert. Diese zeigen die Schönheit unseres Planeten, spektakuläre Luftauf-nahmen und Momente des Lebens im All. Die Ausstellung ist in fünf Stationen gegliedert: Von den intensiven NASA-Trainings bis hin zu spektakulären Bildern der Erde aus dem All. Besucher erleben hautnah den Alltag auf der ISS und die Herausforderungen der Raumfahrt.
Details zur Ausstellung:
• Ort: Ehemaliges K&Ö Home, Murgasse 10, 8010 Graz
• Zeitraum: 1. Februar – 31. März 2025
• Öffnungszeiten: Täglich 10:00 – 18:00 Uhr
• Eintritt: 15 € - 19 € (Tickets online bei Ö-Ticket und vor Ort erhältlich)
Veranstalter
Die Ausstellung wurde von scan.art-Gründer Gottfried Eisenberger, einem der führenden Innovatoren im Bereich digitaler Ausstellungstechnologien, kuratiert und nach Graz ge-bracht.
Für Medienanfragen und weitere Informationen:
Gottfried Eisenberger, MBA
E-Mail: office@viewfromabove.at
Website: www.viewfromabove.at
Telefon: +436603922092
14. Juni 2024
DAS WAR DER FÜNFTE HAGE-AKTIONSTAG - Ganz im Zeichen der Gesundheit
Am 14. Juni 2024 war es wieder soweit: HAGE veranstaltete seinen fünften Aktionstag, der in diesem Jahr ganz im Zeichen der Gesundheit stand. Als Vorreiter in der betrieblichen Gesundheitsförderung in der Region Murtal legte HAGE erneut großen Wert darauf das Wohlbefinden seiner Mitarbeiter zu fördern. „Die Gesundheit und das Wohlbefinden unserer Mitarbeiter haben bei HAGE einen großen Stellenwert, denn nur wenn unser Mitarbeiter gesund und fit sind können sie ihr volles Potenzial entfalten und so maßgeblich zum Erfolg unseres Unternehmens beitragen“, betonte Florian Hampel, Geschäftsführer von HAGE.
Der Aktionstag wurde im Hotel Moselebauer veranstaltet und in Zusammenarbeit mit Sportwissenschaftler Mag.Tom Gmoser und Arbeitspsychologin Mag. Cornelia Hubich Schmon erfolgreich umgesetzt.
Bereits im Vorfeld hatten die Mitarbeiter die Möglichkeit, an umfassenden Voruntersuchungen teilzunehmen. Sie konnten zwischen den Modulen „Bewegungsapparat“ und „Stoffwechsel-Stress und Gewichtsmanagement“ wählen, und je nach Wahl wurden gezielte Messungen durchgeführt. Im Modul „Bewegungsapparat“ wurden die Kraft und Kraftverhältnisse der rumpfstabilisierenden Muskulatur mit dem BackCheck gemessen, der funktionale Defizite und muskuläre Dysbalancen aufdeckt. Zusätzlich wurden eine Wirbelsäulenanalyse und eine S3-Koordinationsmessung vorgenommen.
Das Modul „Stoffwechsel-Stress-Gewichtsmanagement“ umfasste eine Atemgasanalyse zur Bestimmung des Grund-Ruhe-Kalorienumsatzes sowie präzise Informationen über den Fettanteil, Muskelanteil und Wassergehalt des Körpers. Stressanalysen und HRV-Messungen ermöglichten einen umfassenden ganzheitlichen Ansatz. Die Ergebnisse dieser Messungen wurden dann am Aktionstag eingehend analysiert und mit den Teilnehmern besprochen.
Der Tag begann mit einem reichhaltigen Frühstück, das alle auf die bevorstehenden Aktivitäten einstimmte. Interessante Vorträge wie „Ernährung und Bewegung – der Bedarf bestimmt“, „Anatomie verstehen in der Praxis“ und „Leistungsphysiologie verstehen für Kraft- und Ausdauersport“ fesselten die Zuhörer. Praktische Einheiten wie „Lauf-ABC“, „Stabilisationstraining für Ausdauersportler“, „Beinachsen Sprunggelenk/Knie/Hüfte“ und „Wirbelsäulentraining einmal anders“ rundeten das Programm ab. Auch Stressbewältigung und Entspannungstechniken waren wichtige Bestandteile des breitgefächerten Angebots.
In den Pausen sorgte eine Smoothie-Bar für frische Energie, und das Mittagsbuffet stärkte die Mitarbeiter für die nächsten Programmpunkte.
Der Tag fand seinen gemütlichen Ausklang bei Gulasch und Bier, um auch die soziale Komponente nicht zu vernachlässigen. Der Aktionstag bot somit nicht nur die Gelegenheit, gemeinsam an Gesundheit und Wohlbefinden zu arbeiten, sondern stärkte auch den Teamzusammenhalt.
FAZIT:
Der fünfte Aktionstag von HAGE war ein voller Erfolg und unterstrich erneut die Bedeutung von Gesundheit und Wohlbefinden im Unternehmen. Mit einem vielfältigen Programm und speziellen Höhepunkten wurde nicht nur die körperliche Fitness, sondern auch der Teamgeist gefördert. Ein Tag, der in Erinnerung bleibt und die Basis für zukünftige Gesundheitsinitiativen legt.
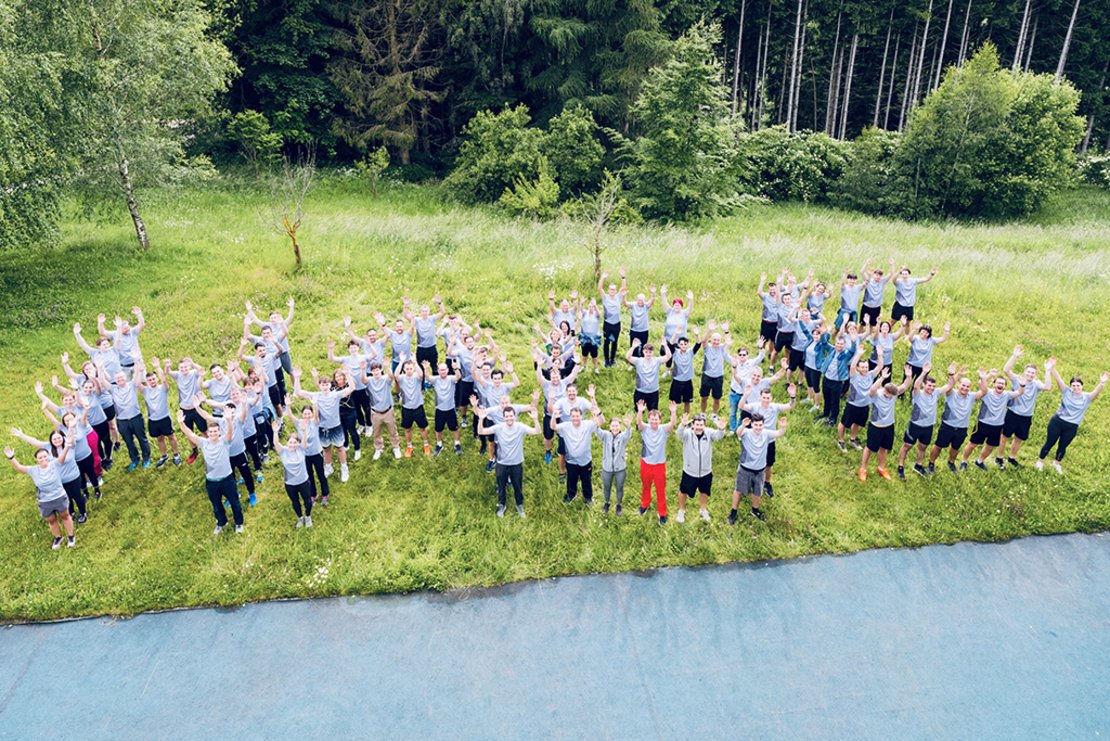
29. Jänner 2024
Chancengleichheit, Fairness & Gleichstellung stehen bei HAGE im Fokus
HAGE Sondermaschinenbau GmbH wurde vom Bundesministerium für Wirtschaft und Arbeit mit dem equalitA-Gütesiegel für besonderes Engagement in der innerbetrieblichen Frauenförderung ausgezeichnet.
Damit zählt HAGE zu den erfolgreichen Unternehmen, die Frauen fördern, dies sichtbar machen und die berufliche Gleichstellung aller Geschlechter unterstützen und fördern. Es freut uns sehr, dass Werte wie Chancengleichheit, Fairness & Gleichstellung im Unternehmen gelebt und auch nach außen getragen werden.
Die Einführung von Maßnahmen wie der 4-Tage-Woche zeigt, dass HAGE sich aktiv für die Work-Life-Balance seiner Mitarbeiterinnen und Mitarbeiter einsetzt. Diese Maßnahmen tragen dazu bei, die Vereinbarkeit von Karriere und Familie zu verbessern, insbesondere für Frauen, die oft vor der Herausforderung stehen, beides in Einklang zu bringen.
Wir sind der Überzeugung, dass Chancengleichheit nicht nur ein Schlagwort ist, sondern ein Grundprinzip, das den Erfolg bestimmt.
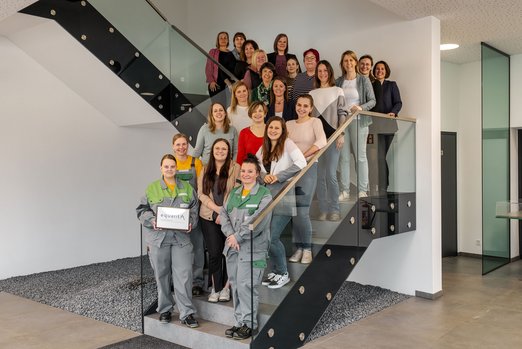
14. Juni 2023
Großaufträge für die Bahnindustrie
Nachdem erst im Februar der größte Auftrag der Firmengeschichte verzeichnet wurde, konnte das HAGE Team weitere neue Großaufträge aus der Bahnindustrie an Land ziehen. Der Gesamtwert der Aufträge beläuft sich auf ca. 15 Millionen Euro.
Fast zeitgleich haben sich zwei Global Player der Schienenindustrie, darunter Stadler Rail aus der Schweiz, dazu entschlossen, ihre neuen innovativen Projekte mit Hage umzusetzen. Wie in der Luft- und Raumfahrt und der Automobilindustrie ist der Leichtbau auch in der Schienenindustrie ein unabdingbares Muss, um einen möglichst ressourcenschonenden und umweltfreundlichen Personentransport zu erreichen. Hand in Hand mit Leichtbaudesign aus Aluminiumlegierungen geht das neue Schweißverfahren FSW (Friction Stir Welding – Rührreibschweißen), bei dem Hage zu den Weltmarktführern zählt und sowohl Anlagen- als auch Prozesstechnik liefert.
Ein Branchenführer der Bahnindustrie vertraut bei der Produktion moderner Hightech-Waggons bereits seit Jahren auf die Qualität und das Know-How von HAGE. Hier wird der bestehende Maschinenpark um zwei weitere HAGE Anlagen erweitert. Dabei handelt es sich konkret um zwei hybride Portalzentren, mit denen die Großkomponenten sowohl gefräst als auch geschweißt werden können. Mitgeliefert wird ein sogenannter „Digitaler Zwilling“, an dem das Bearbeitungsprogramm vorab abgefahren werden kann, um Kollisionen zu vermeiden und die Durchlaufzeit zu optimieren.
Nahezu zeitgleich orderte das Schweizer Unternehmen Stadler Rail FSW Anlagen zur Bearbeitung von Aluminiumkomponenten für Doppelstocktriebzüge. Um die Kapazitäten abdecken zu können, wurden gleich zwei der leistungsstarken FSW Anlagen bestellt.
Und auch sonst tut sich bei HAGE einiges. Momentan werden zwei Fertigungslinien zur Komponentenherstellung von Batteriewannen für Elektroautos eines deutschen Premium-Autoherstellers fertiggestellt. Zwei weitere Produktionsanlagen eines anderen Herstellers haben das Werk kürzlich verlassen und werden aktuell in Deutschland in Betrieb genommen bzw. nach Mexiko verschifft.
18. Februar 2023
Rekordauftrag nach Obdach geholt
Text: Manfred Neuper, Kleine Zeitung
Das Familienunternehmen Hage Sondermaschinenbau mit Sitz in Obdach hat einen spektakulären Auftrag über 20 Millionen Euro an Land gezogen.
Vorbereitungen, Konzeptfindungen, Machbarkeitsstudien und die Angebotsausarbeitung - eineinhalb Jahre hat all das letztendlich gedauert. ,,Es war eine intensive Zeit, aber es hat sich ausgezahlt." Dafür hat Stefan Hampel auch eine in Zahlen gegossene Unterfütterung parat: Hörbar stolz berichtet der Geschäftsführer von Hage Sondermaschinenbau mit Sitz in Obdach von einem Auftragsvolumen von mehr als 20 Millionen Euro - ,,es ist der größte Auftrag unserer Firmengeschichte".
Für einen großen deutschen Bausystemspezialisten werden drei Hightech-Anlagen für die Produktion von Schalungselementen geliefert. ,,Es handelt sich dabei um die vollautomatische Fertigung von Stahlprofilen, die eine Vielzahl von Bearbeitungsstationen durchlaufen und anschließend verschweißt werden." Die Anlagen, die mit 50 Metern Länge und rund 16 Metern Breite ,,ordentliche Geräte" sind, wie es Hampel ausdrückt, kombinieren Sägeaggregate, Stanzwerkzeuge, Umformprozesse und Montageautomaten mit Bauteilzuführung. Eine besondere Rolle spiele die „Bauteilkontrolle mittels Messsystemen und Qualitätsinspektion durch entsprechende Sensorik". Ebenfalls inklusive: eine ständige Verschleiß überwachung, um auch eine vorbeugende Wartung zu ermöglichen. Dafür zeichne ein eigens bei Hage entwickeltes Softwaretool verantwortlich, so Hampel. Die historische Dimension des Auftrags macht auch die Relation zum Jahresumsatz des knapp 140-köpfigen Unternehmens deutlich: Dieser lag zuletzt bei rund 24 Millionen Euro. ,,Gerade in gesamtwirtschaftlich herausfordernden Zeiten ist so eine Grundauslastung sehr gut für uns", so Hampel. Denn die Anlagen werden nun Schritt für Schritt montiert „und uns die beiden nächsten Jahre beschäftigen". Wie berichtet, ist für Platz und Ressourcen gesorgt - Hage hat Millionen in ein zweites Produktionswerk in Obdach investiert.
In diesem zweiten Werk zeige sich zudem, warum wir auch im Bereich des Rührreibschweißens als Technologieführer gelten". Für Batteriewannen, die in Elektroautos eingebaut werden, sind vom Familienunternehmen zwei Anlagen entwickelt worden, die mit sechs Schweißaggregaten gleichzeitig von zwei Seiten die Einzelteile verbinden", so Hampel. Durch dieses innovative und welteit einzigartige Anlagenkonzept werden der Schweißverzug und die Produktionszeit minimiert." Auch die Intensivbeziehung zur Europäischen Weltraumagentur ESA wird weiterhin gepflegt. So wird demnächst eine hochrangige Delegation eintreffen, weil auf Hage-Anlagen in Obdach im Zuge eines groß angelegten Forschungsprojekts ein neues 3D-Druckverfahren getestet wird, über das sich Substrate auf gewellten Flächen anschweißen lassen, wie Hampel erläutert.
1. August 2021
FERTIGSTELLUNG WERK2
Nach 21 Monaten Bauzeit wurde das neue Bürogebäude fertiggestellt und von den ersten Mitarbeitern bezogen.
Das Bürogebäude mit einer Gesamtfläche von 1000 m² bietet vorerst Platz für 20 Arbeitsplätze. Das zweite Obergeschoss kann bei Bedarf jederzeit weiter ausgebaut werden. Im zweiten Stock befindet sich darüber hinaus ein großer Konferenz- und Schulungsraum mit 20 Plätzen, der vor allem für interne Weiterbildungen der MitarbeiterInnen genutzt wird. Das Herzstück des Gebäudes bildet das neue, firmeneigene Fitnessstudio im ersten Obergeschoss. Auf den 150 m² können die Mitarbeiter zukünftig nach Herzenslust trainieren oder am angebotenen Kursprogramm teilnehmen. „Beim Neubau haben wir großen Wert auf eine offene, angenehme Atmosphäre gelegt, in der sich unsere Mitarbeiter und Mitarbeiterinnen und natürlich auch unsere Kunden wohlfühlen. Außerdem wurde das Bürogebäude so konzipiert, dass wir es bei Bedarf einfach erweitern können“, so Geschäftsführer Florian Hampel.
Bereits im November 2019 konnte die angrenzende, 1800 m² große Montagehalle in Betrieb genommen werden. Neben Kundenprojekte aus dem Sondermaschinenbau werden in der neuen Halle auch die industriellen 3D Drucker von HAGE3D gefertigt.
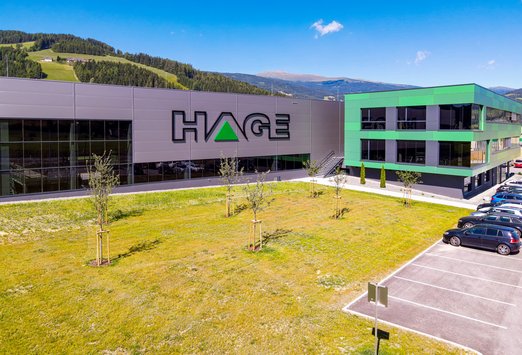
Dieses Projekt wird aus Mitteln des Europäischen Fonds für regionale Entwicklung kofinanziert.
Nähere Informationen zu IWB/EFRE finden Sie auf www.efre.gv.at.
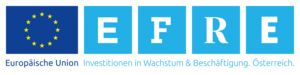
27. September 2021
STARTSCHUSS FÜR DIE HAGE LEHRWERKSTÄTTE
Seit September 2021 setzt HAGE bei der Lehrlingsausbildung auf eine eigene Lehrwerkstätte. Derzeit werden beim Obdacher Sondermaschinenbauer insgesamt 21 Lehrlinge in den Bereichen Mechatronik, Maschinenbautechnik und Zerspanungstechnik ausgebildet.
Die Lehrlingsausbildung hat bei HAGE seit jeher einen hohen Stellenwert. „Unsere bestens ausgebildeten Mitarbeiterinnen und Mitarbeiter sind der Grundstein unseres Erfolges. Um für die Zukunft gut aufgestellt zu sein und dem Trend des Fachkräftemangels entgegenzuwirken, haben wir uns entschieden, die Lehrlingsausbildung bei HAGE weiter auszubauen und in eine Lehrwerkstätte zu investieren“, so HAGE Geschäftsführer Peter Freigassner-Sanchez.
KARRIERE MIT LEHRE BEI HAGE
Die im Sommer 2021 fertiggestellte Lehrwerkstätte wurde in die, im Jahr 2019 errichtete, 1800 m² große Halle integriert. Bei der Ausbildung setzt HAGE gezielt auf eine abwechslungsreiche Mischung aus Theorie und Praxis. Die Jugendlichen arbeiten bereits während ihrer Lehrzeit an laufenden Projekten mit und übernehmen früh selbstständig Aufgaben. Die Grundausbildung erfolgt seit September 2021 in der eigenen Lehrwerkstätte. Ausgestattet mit Schweißkabinen, Werkbänken, einer Schleifkabine, einer Ständerbohrmaschine, einer umfangreichen Festo-Schalttafel für Pneumatik und Hydraulik wie auch Elektrik und vielem mehr, bietet die Lehrwerkstätte beste Voraussetzungen für die Ausbildung der jungen Fachkräfte. In den ersten Wochen werden dort metalltechnische Grundlagen vermittelt und der geschickte Umgang mit Feile, Säge, Bohrer und Messtechniken erlernt. Die Schulung an CNC- und Drehmaschine erfolgt, möglichst praxisnah, direkt in der Fertigung. Für die theoretische Ausbildung wurde in zusätzliche Schulungsräume investiert. Neben dem fachlichen Wissen werden auch soziale Inhalte vermittelt und das kollegiale Miteinander gestärkt. Der Lehrberuf des Mechatronikers wird zukünftig vertiefend in Hardware, Planung und Softwareentwicklung ausgerichtet werden. So erfolgt auch hierfür die Ausbildung zur Gänze bei HAGE.
Nach dem Motto „Karriere mit Lehre“ eröffnen sich nach erfolgreichem Lehrabschluss gute Weiterentwicklungsmöglichkeiten und Karrierechancen. Zahlreiche Führungspositionen im Unternehmen sind mit Mitarbeitern besetzt, die bei HAGE die Lehre absolviert haben. Bereits während der Ausbildung werden gute Leistungen und Engagement belohnt. Und auch sonst hat das Familienunternehmen viel zu bieten. Neben regelmäßigen Weiterbildungsmaßnahmen, Sportveranstaltungen und Firmenfeiern gibt es seit 2021 auch ein firmeninternes Fitnessstudio für die Mitarbeiterinnen und Mitarbeiter.
NEUES STUDIENANGEBOT IM MURTAL
Ab dem Herbst 2022 wird HAGE außerdem die Räumlichkeiten für ein neues Studienangebot im Murtal bereitstellen. Die Kooperation der Grazer Fachhochschule Campus02 und der Wirtschaftsinitiative „Kraft.Das Murtal“ hat 15 Studienplätze für den berufsbegleitenden Bachelorstudiengang Automatisierungstechnik geschaffen. Starten wird der Studiengang im Wintersemester 2022/2023. „Um für die Zukunft gut aufgestellt zu sein, brauchen wir gut ausgebildete Mitarbeiterinnen und Mitarbeiter. Dass der Bachelorstudiengang Automatisierungstechnik zukünftig im Murtal bei HAGEangeboten wird, ist eine enorme Aufwertung für die ganze Region“, freut sich Florian Hampel, HAGE Geschäftsführer und Sprecher der Initiative "Kraft.Das Murtal".
Schülerinnen und Schüler die sich für eine Lehre bei HAGE interessieren, können gerne vorab einen Schnuppertag absolvieren und dabei das Unternehmen besser kennenlernen. Anmeldungen sind ab sofort telefonisch unter +43 3578 2209 213 oder per Mail an bewerbungen@hage.at möglich. Auch für den Studiengang werden bereits Bewerbungen entgegengenommen. Weitere Informationen erhalten Sie unter kraft@dasmurtal.at oder unter at@campus02.at.
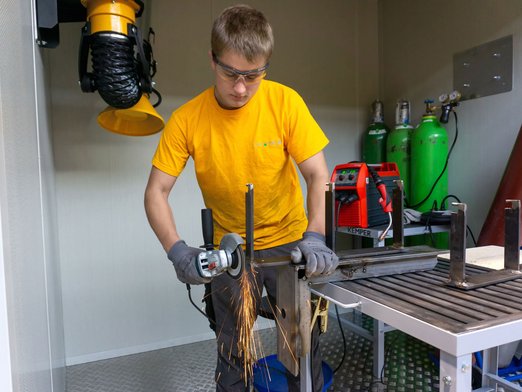
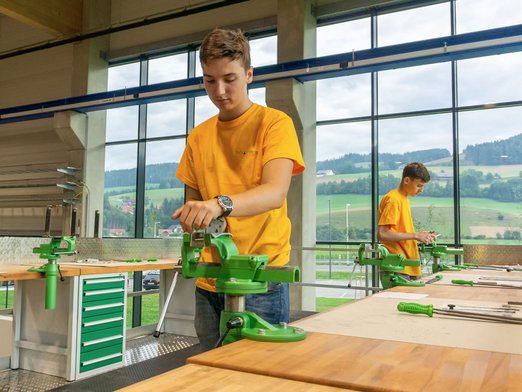
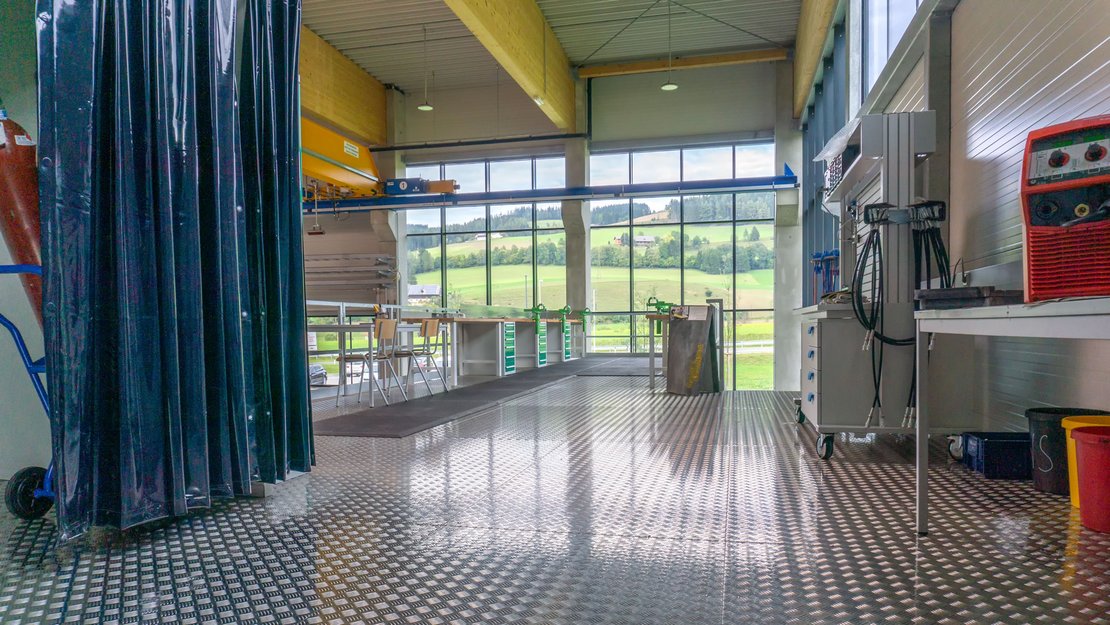
Die neue Montagehalle wird aus Mitteln des Europäischen Fonds für regionale Entwicklung kofinanziert.
Nähere Informationen zu IWB/EFRE finden Sie auf www.efre.gv.at.
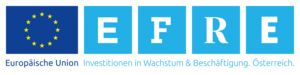
09. Juli 2021
LEISTUNGSSTARKE FSW ANLAGE
FÜR SIEMENS MOBILITY AUSTRIA GMBH, WERK SIMMERING
Zum Bau von hochmodernen U-Bahn Flotten entwickelte HAGE in Zusammenarbeit mit Siemens Technikern eine neue FSW Anlage.
Im November 2018 sichert sich Siemens einen Großauftrag zur Erneuerung einer der ältesten U-Bahnlinie. Die neuen Metrozüge modernisieren das Reisen für Millionen von Fahrgästen in einer der beliebtesten Metropholen Europas. Zur Produktion der U-Bahn-Züge setzt Siemens auf eine der leistungsstärksten Rührreibschweißanlage von HAGE.
Herzstück der Anlage ist der von HAGE entwickelte FSW-Kopf mit integrierter Kraftmessung in allen Achsen und innen liegender V-Achse. Dieser überwacht und regelt permanent den Schweißprozess und gewährleistet den Maschinenschutz. Erstmals zum Einsatz kommt der neu entwickelte, integrierte Werkzeugwechsler für geteilte FSW-Werkzeuge. Er reduziert die Nebenzeiten und ermöglicht eine effiziente Automatisierung. Bei der Steuerung greift HAGE erstmalig auf die Siemens Sinumerik- One zurück. Eine von HAGE entwickelte Software WeldCheck überwacht den Schweißprozess. Die Software erfasst alle Prozessparameter, zeichnet diese auf und wertet die Daten in Echtzeit aus.
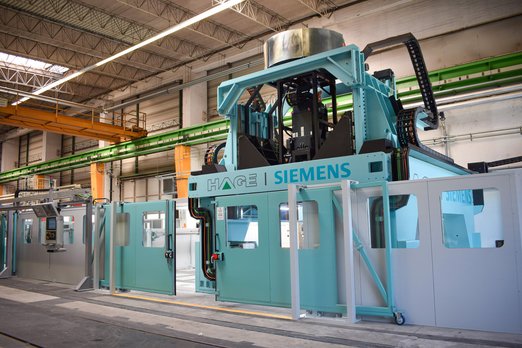
Mitte September 2020 erfolgte die Übergabe der Anlage an Kunden in Wien. Zeitgleich erweiterten wir das HAGE Kompetenzzentrum um eine baugleiche Maschine, die die FSW Entwicklung weiter vorantreibt.
Entwicklung komplexer Spannvorrichtungen samt Prozessentwicklung
Nachträglich beauftragte der Kunde die gemeinsame Entwicklung diverser Spannvorrichtungen. Das Projekt beinhaltet:
- Vorstudien zur Evaluierung von Prozesskräften,
- Vorhaltungen,
- Vorspannungen,
- berücksichtigen von Arbeitsräumen und Restriktionen der Maschine,
- fundierte FSW Werkzeug- und Prozessentwicklung bis hin zur
- programmieren der NC-Codes basierend auf den Schweißabfolgen.
Unser Partner Siemens Mobility Wien begleitet und unterstützt uns während der Projektierung aktiv. Damit verkürzen wir die Integrationszeit von der Lieferung bis zur Produktion. Die baugleiche Anlage in Obdach ermöglicht uns im Vorfeld mit Tests und Schulungen zu starten und erste Bauteile zu liefern. Dieses Vorgehen beschleunigt den Entwicklungsprozess und garantiert risikominimierte Durchlaufzeiten.
Ein besonderes Highlight ist eine Vorrichtung, die das Bauteil nach dem Rührreibschweißen bei Bedarf vollautomatisch vermisst und ausrichtet. Ein Renishaw Messtester vermisst die neuralgischen Punkte am Werkstück. Ein von HAGE entwickelter Algorithmus berechnet anschließend, welche Schweißkraft an den einzelen Stellen aufzuwenden ist, um ein ebenes Bauteil herzustellen.
10. Mai 2021
BIS ZU 500 PROFILTYPEN VOLLAUTOMATISCH BEARBEITET
Bei HAGE ist jedes Projekt eine (neue) Herausforderung. Auf das HAGE Bearbeitungszentrum für die Firma Josko trifft der Spruch in vielerlei Hinsicht zu. Bereits im Februar 2019 starteten Mitarbeiter mit der Entwicklung der Anlage. Nach arbeitsreichen Monaten konnte der Kunde im Dezember 2020 die Anlage in Betrieb nehmen. Markus Steinkellner (Steuerungstechnik) und Christian Feßl (Montageleiter) waren maßgeblich am Anlagenaufbau beteiligt und gewähren aus erster Hand einen Einblick in das Projekt.
Vollautomatische Bearbeitung von Fensterprofilen im HAGE Bearbeitungszentrum
Nach der manuellen Zufuhr der Werkstücke vermisst am Ende des Einlaufförderers ein Sensor die Profile in Länge, Breite und Höhe. Die HAGE Lösung erkennt den Profiltyp und wählt für die nächsten Stationen automatisch die Arbeitsschritte aus. Insgesamt fünf vierachsige NC Vorschubzangen transportieren die Werkstücke durch die Anlage.
Das erste von zwei Bearbeitungszentren ist mit acht Spindeln ausgestattet. Nach der Bearbeitung wird das Profil durch eine Vorschubzange zur nächsten Station transportiert - dem Sägezentrum. Die 5-Achs Säge führt abhängig vom Profil Geradschnitte, Gehrungsschnitte oder Shifterschnitte durch. Anschließend wird das Werkstück weiter zum zweiten Bearbeitungszentrum transportiert.
Ausgestattet mit einem automatischen, 40-fachen Werkzeugwechsler wird– je nach Type – gefräst, gebohrt oder gesägt. Mit einem 5-Achs Bearbeitungskopf werden dabei auch stirnseitige Bearbeitungen ausgeführt. Anfallende Späne oder Abschnitte werden automatisch abtransportiert und sortenrein getrennt. Der Abschnittsgreifer fördert die fertigen Fensterprofile zum Auslaufpuffer. Die Entnahme der Fertigteile erfolgt manuell durch den Anlagenbediener.
Das vollautomatische Bearbeitungszentrum verknüpft verschiedene Technologien zu einer Gesamtanlage. Trotz des Erfahrungsschatzes der HAGE Mitarbeiter tauchen immer wieder neue Aufgabenstellungen auf. Bei diesem Projekt lagen die Besonderheiten vor allem in der Steuerungstechnik, wie Markus Steinkellner erzählt: „Die komplexe Anlage ist mit zwei Sinumerik-Steuerungen ausgestattet. Sie werden zwar eigens in Betrieb genommen, müssen aber untereinander kommunizieren. Die Bearbeitungsprogramme hat zur Gänze der Kunde erstellt. Die Steuerung haben wir übernommen – das hatten wir so auch noch nie. Auch die Messsensorik ist sehr umfangreich. Bassierend auf den vermessenen Daten weiß die Anlage, welches Profil vorliegt und welche Bearbeitungsschritte benötigt werden. Derzeit bearbeiten wir 88 unterschiedliche Typen. Bei Bedarf können wir auf bis zu 500 erhöhen.“ Christian Feßl sieht das ähnlich: „Die Anlage ist hochgradig komplex. Umso wichtiger ist es, dass alle Komponenten punktgenau verarbeitet sind bzw. verbaut werden. Hinzu kam noch die Coronasituation. Laufend mussten wir auf neue Verordnungen reagieren.“
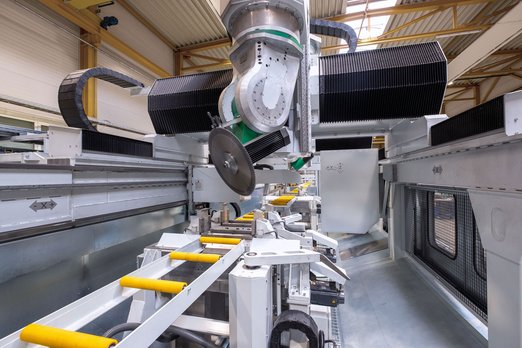
5-Achs-Säge für Geradschnitte, Gehrungsschnitte oder Schifterschnitte
Anlagenhighlights:
- Oberflächenschonende Werkstückbearbeitung
- Bis zu 500 verschiedene Profilgeometrien
- Maschinengenauigkeit:± 0,1 mm pro 3 m
- Achsgeschwindigkeiten bis 3m/s
- Spindeldrehzahlen bis 24.000 U/min
- Werkzeugwechselzeit BAZ 1 ca. 1s
- Steuerung: 2 Stück SINUMERIK 840D sL
- 72 Servoachsen
- 40-fach Werkzeugwechsler inkl. RFID
- 2-fach Sonderwerkzeugwechsler für Sägeblätter bis Ø 650 mm
- Werkzeugbruchkontrolle
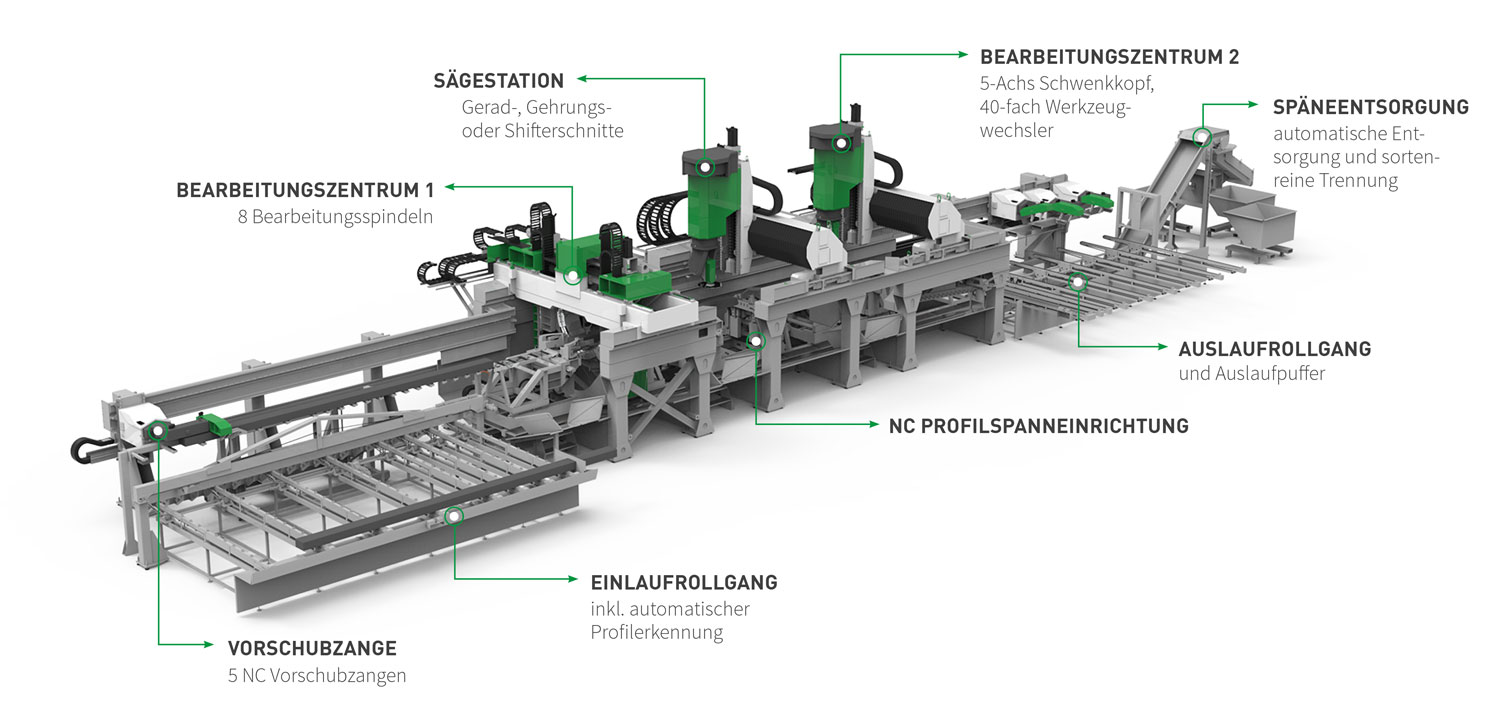
Modernes Bearbeitungszentrum mit zwei Bearbeitungsstationen und einer Sägestation
10. April 2020
HAGE Sondermaschinenbau und HAGE3D entwickeln druckkontrolliertes Beatmungsgerät
Im Kampf gegen die Coronavirus-Pandemie entwickeln HAGE Sondermaschinenbau und HAGE3D in enger Zusammenarbeit mit der Medizinischen Universität Graz ein druckkontrolliertes Beatmungsgerät.
In Österreich wird derzeit intensiv an Lösungsansätzen zur Eindämmung der COVID-19 Pandemie geforscht. Da es weltweit derzeit vor allem bei medizinischen Produkten regelmäßig zu Versorgungsengpässen kommt, ist ein Ziel der österreichischen Initiative die Entwicklung einer kurzfristig verfügbaren, druckkontrollierten Beatmungsform für Krisen- bzw. Notsituationen.
Bei HAGE Sondermaschinenbau und HAGE3D hat man daher in den letzten zwei Wochen intensiv an der Entwicklung zweier Prototypen gearbeitet. Den Innovationsgeist und die Präzision des Familienunternehmens will man bei HAGE nun für die rasche Bekämpfung der Folgen des Coronavirus nützen. An sich ist HAGE Sondermaschinenbau für 5-Achs Bearbeitungsanlagen und Rührreibschweißlösungen für die Raumfahrt und Schienentechnologie bekannt. Das Schwesterunternehmen HAGE3D, das wie auch HAGE im Eigentum der Familie Hampel steht, hat durch die Prototypenentwicklung eines Implantat-3D-Druckers bereits erste Erfahrungen in der Medizintechnik gesammelt.
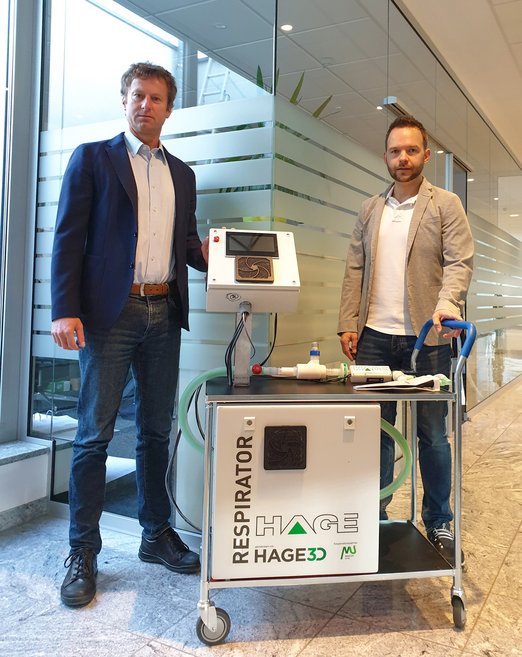
DI Stefan Hampel und DI Peter Freigassner-Sanchez und das von HAGE Sondermaschinenbau und HAGE3D entwickelte Beatmungsgerät.
Erste Varianten auf Basis eines Beatmungsbeutels und eines Pneumatikzylinders wurden vom Geschäftsführer DI Peter Freigassner-Sanchez entwickelt, gedruckt und getestet. Zusammen mit dem HAGE3D Team entstand schlussendlich eine funktionstüchtige, überwachte Maschine. Die Anforderungen und der Aufbau werden in enger Zusammenarbeit mit Experten der Medizinischen Universität Graz in mehreren Iterationen verfeinert. Jüngste Testergebnisse - mit Prof. Dr. Horst Olschweski, Abteilungsleiter der Pulmonologie in Graz, sind sehr vielversprechend.
Der Druck der Sauerstoffzufuhr wird dabei über ein patientennahes Ventilsystem im Beatmungsschlauch geregelt und durch Sensoren kontrolliert. Die übermittelten Werte werden grafisch auf dem Touchdisplay angezeigt. Ein visuelles und akustisches Warnsystem meldet die Abweichung von definierten Sollwerten. Zur Sicherstellung der Hygieneanforderungen sind zahlreiche Komponenten aus medizinischen Einwegmaterialien gefertigt und werden vor jedem Patienten getauscht bzw. gereinigt. Komponenten, die nicht in Kontakt mit dem Patienten kommen, werden mittels hygienischer Flächendesinfektion gereinigt. Funktionstests wurden bereits durch Versuchsreihen verifiziert.
IV-GF Gernot Pagger hat das Potential bzw. die Wichtigkeit der Entwicklung erkannt und HAGE wurde innerhalb der COVID19 Krisen Task Force von Prof. Ramsauer (TU Graz) zum Leader für die Entwicklung von Notfall-Beatmungsgeräten bestellt. Die COVID19 Krisen Task Force steht dazu in enger Abstimmung mit Frau Minister Schramböck.
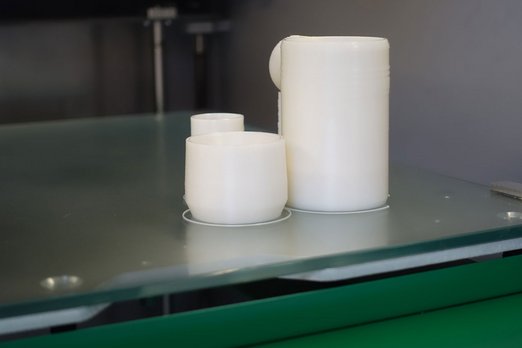
Additiv gefertigte Komponenten für das Beatmungsgerät mit dem 3D-Drucker von HAGE3D.
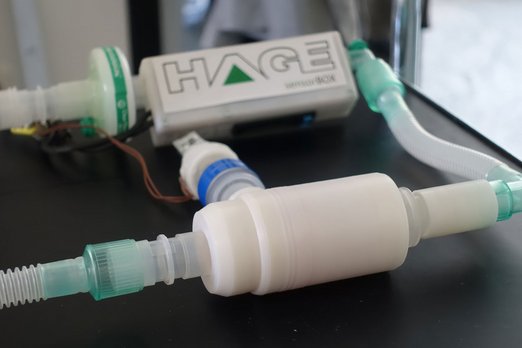
Ein 3D gefertigtes Ventil steuert die Druckzufuhr des Sauerstoffs.
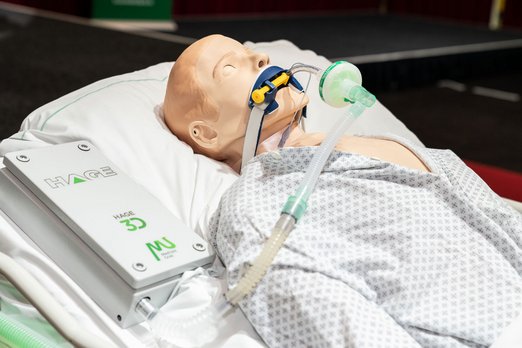
Demonstration am Dummy. Foto: Land Steirmark/Streibl
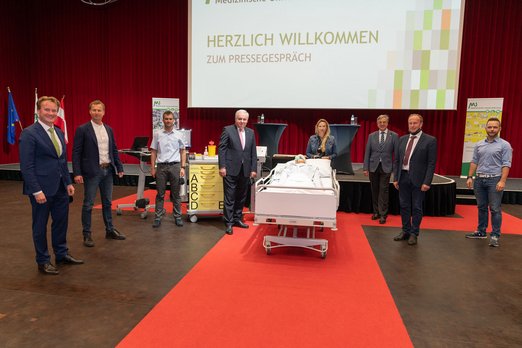
Präsentation des Beatmungsgeräts. Foto: Land Steirmark/Streibl
10. März 2020
HAGE baut zusätzliches Werk in Obdach
Nach einem Bürozubau 2012/2013 startet das Familienunternehmen HAGE im Frühjahr 2019 ein neues Bauvorhaben.
Bis Ende 2020 entsteht, angrenzend an das bestehende Firmengelände, eine großzügige Industriehalle mit Bürofläche.
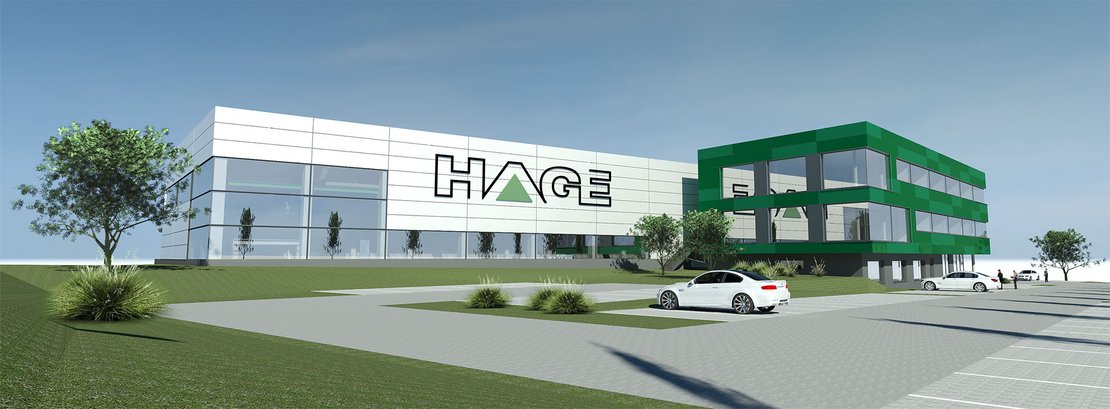
Eine breite Produktpalette und laufende Produkterweiterungen haben in den letzten Jahren zu einem kontinuierlichen, gesunden Wachstum geführt. Neue Technologien, wie Rührreibschweißen (FSW) und Additive Fertigung (3D-Druck) beschleunigen das Wachstum zusätzlich.
NEUE MONTAGEHALLE FÜR
GROSSPROJEKTE UND 3D-DRUCK
Damit auch zukünftig genug Fläche für die immer größer werdenden Kundenanlagen zur Verfügung steht, wird im April mit dem Bau einer neuen Montagehalle begonnen. Diese bietet in der ersten Ausbaustufe Platz für über 800 m² Bürofläche sowie eine 1800 m² große Industriehalle mit zwei Schwerlastkränen und einer Hallenhöhe von 12 m. Der Geschäftsbereich Additive Fertigung (HAGE 3D) wird mitsamt Montage und Administration in den Neubau übersiedeln. Seit den ersten „Gehversuchen“ 2014 hat sich der Bereich 3D-Druck sehr gut entwickelt und es konnten 14 neue Arbeitsplätze geschaffen werden.
„Der Neubau bietet uns die Möglichkeit, auch unsere Großanlagen sowie Industriedrucker weiterhin hier am Standort in Obdach zu produzieren und die bestehenden Arbeitsplätze zu sichern. Aktuell verfügen wir über knapp 6.000 m² Produktionsfläche. Mit der Expansion können wir in mehreren Stufen auf über 10.000 m² ausbauen. Wir sind mit der Region sehr verbunden und schätzen die Qualität unserer Fachkräfte“, so Florian Hampel zu dem Bauvorhaben.
Die steirische Wirtschaftslandesrätin Barbara Eibinger-Miedl betonte anlässlich des Spatenstichs für die neue Halle: „HAGE ist ein bedeutender regionaler Leitbetrieb. Die aktuelle Erweiterung ist eine wichtige Zukunftsinvestition, durch die der Standort Obdach abgesichert, bestehende Arbeitsplätze erhalten und neue geschaffen werden. Das sorgt für Lebensqualität und stärkt die Region nachhaltig. Ich danke Florian und Stefan Hampel und dem gesamten HAGE-Team für dieses starke Bekenntnis zum Wirtschaftsstandort Steiermark!“
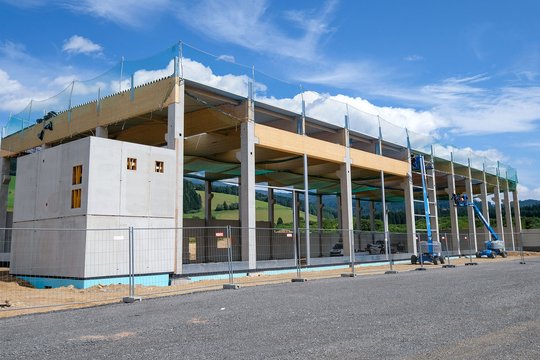
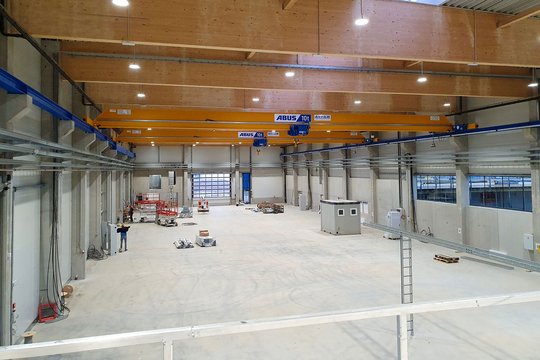
INVESTITIONEN IN DIE ZUKUNFT DER MITARBEITER
Um die Aus- und Weiterbildung neuer und bestehender Mitarbeiter zu fördern, wird in der neuen Halle in Schulungsräumlichkeiten investiert. In der HAGE Akademie sollen junge Mitarbeiter vom Erfahrungsschatz älterer Kollegen sowie externer Experten profitieren. Im Obergeschoß wird ein betriebseigenes Fitnessstudio für die Mitarbeiter entstehen. Damit wird das Angebot an gesundheitsfördernden Maßnahmen erweitert und der Stellenwert im Unternehmen weiter gestärkt. Dank der Investition in den bestehenden Firmenstandort, werden nicht nur die knapp 130 Arbeitsplätze gesichert, sondern auch attraktive, neue Stellen geschaffen.
Daten und Fakten:
Investitionsvolumen: 8 Mio. EURO
Hallenfläche: 1.800 m²
Bürofläche: 800 m²
Fertigstellung: Ende 2019
Dieses Projekt wird aus Mitteln des Europäischen Fonds für regionale Entwicklung kofinanziert.
Nähere Informationen zu IWB/EFRE finden Sie auf www.efre.gv.at.
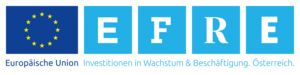
5. Februar 2020
VON OBDACH INS WELTALL
Durch die Kombination innovativer Fertigungstechniken mit bewährten Lösungen hat HAGE den Schritt in die internationale Raumfahrt geschafft und die Bewährungsprobe erfolgreich bestanden.
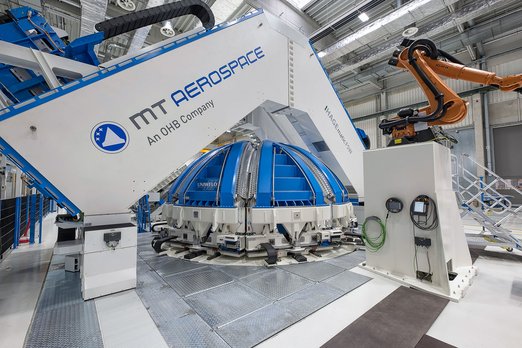
Auf den individuellen Sondermaschinen werden die Verschlusskappen der Raketentanks mittels FSW-Verfahren hochpräzise verschweißt.
Die Raumfahrtindustrie gilt als die Königsklasse der Industrie. Nur wenige Betriebe schaffen es tatsächlich, in der komplexen und hart umkämpften Sparte Fuß zu fassen. Nicht umsonst gilt sie auch als fortschrittlichste Branche der Welt.
Den Zulieferern wird einiges abverlangt. So werden modernste Fertigungsanlagen und maximale Qualität gefordert, weiß man bei HAGE aus Erfahrung. 2016 ist dem Familienunternehmen aus Obdach der Sprung in die höchste Liga gelungen. Der Augsburger Luft- und Raumfahrtspezialist MT Aerospace unterzeichnete einen Millionen-Vertrag. Die 50 m lange Anlage ist eine Sonderanfertigung und wird zur Bearbeitung von Verschlusskappen (Bulkheads) für Raketentanks des europäischen Raumfahrtprogramms eingesetzt.
Nicht nur für HAGE sondern auch für den Auftraggeber war das Projekt eine neue Herausforderung. Für die Fertigung der komplexen Komponenten wurden Konzepte und Lösungen folgend der Industrie 4.0 Systematik eingeführt und ein neues Schweißverfahren implementiert. Das Ergebnis: dreimal so effiziente Produktionsabläufe und deutliche Kosteneinsparungen. Das Kernstück des Produktivitätsfortschritts und der technologischen Weiterentwicklungen ist die von HAGE gelieferte FSW-Anlage. Sie wurde 2018 installiert und ist bislang weltweit einzigartig. FSW steht für Friction Stir Welding, auf Deutsch Rührreibschweißen. Dabei handelt es sich um ein Festphasenfügeverfahren, das Werkstoffkombinationen die bislang als nicht oder sehr schwer verschweißbar galten, miteinander verbindet. Im Fall von MT Aerospace sind das spezielle Aluminiumlegierungen. Im Vergleich zum konventionellen Schweißverfahren wird beim FSW-Prozess eine deutlich geringere thermische Eigenspannung erzeugt. Dadurch lassen sich dünnere Wandstärken verschweißen, was folglich zu beträchtlichen Gewichtseinsparungen führt und einen entscheidenden Vorteil in der Luft- und Raumfahrt bringt.
Das innovative Verfahren eignet sich optimal für den leistungsfähigen Leichtbau und überzeugt zugleich mit hoher Nahtfestigkeit. Die HAGE FSW-Anlage punktet nicht nur mit fertigungstechnischen Vorteilen sondern auch mit erheblicher Zeiteinsparung. Der bisherige Schweißvorgang dauerte rund zehn Minuten, die Vorbereitung dafür aber mehr als drei Stunden.
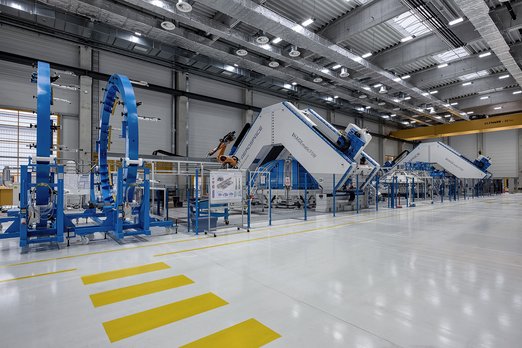
Zur Herstellung von Raketentanks für die europäische Raumfahrt lieferte HAGE zwei 50 m lange FSW-Anlagen.
Mit der neuen Maschine werden die Vorbereitungszeiten deutlich verkürzt. Zudem werden sämtliche Prozesse von der Anlage überwacht, dokumentiert und die Bauteile zerstörungsfrei per Ultraschall untersucht. Verlassen die Komponenten - in diesem Fall die Bulkheads - die FSW-Anlage, sind sie bereits fertig bearbeitet und überprüft. Ein enormer Technologiesprung, den die Geschäftsführung von MT Aerospace auf eine Größenordnung von rund 20 Jahren schätzt.
Neben der Anlage für Augsburg erhielt HAGE von MT Aerospace den Folgeauftrag zur Entwicklung und Produktion einer weiteren FSW-Anlage. Diese wird am Standort in Bremen zur Bearbeitung von Oberstufentanks europäischer Raketen eingesetzt. Auch weitere, weltweite Weltraumorganisationen sind auf HAGE aufmerksam geworden. Bei Terminen im hauseigenen FSW Kompetenzzentrum in Obdach hat sich beispielsweise eine Abordnung von „Roskosmos“ von der FSW Kompetenz des Unternehmens überzeugt.
„Die Grenzen der FSW-Technologie werden bei uns stets erweitert. Wir vereinen Innovationsgeist und Umsetzungsexpertise. Das gewährleistet, dass die Qualität nicht erst in der Ausführung, sondern schon in der Planung in unserer Hand liegt“, sagt DI Peter Freigassner-Sanchez, technischer Geschäftsführer von HAGE.
Mit der Wahl der HAGE FSW-Anlage setzte MT Aerospace 2016 auf einen bislang in der Branche noch unbekannten Zulieferer. Doch die Kompetenz und die jahrelange Erfahrung im Anlagenbau konnten das international führende Luft- und Raumfahrtunternehmen überzeugen. Beeindruckend war auch der Einsatz modernster Methoden und Techniken in der Angebots- und Engineeringphase. Mit 3D CAD-Technik und mit Hilfe von „Virtual Reality“ wurde der Auftraggeber bereits vorab durch die virtuelle Anlage geführt und konnte das Maschinenkonzept in seiner Gesamtheit erleben. Nicht zuletzt überzeugten auch die „Soft Skills“- HAGE punktete mit seinem innovativen und motivierten Team aus Experten, das schnell zeigte, dass es den hohen technischen Anforderungen und der Dynamik des Projektes gerecht wird.