29th of january 2024
EQUAL CHANCES, FAIRNESS & DIVERSITY ARE A FOCUS AT HAGE
HAGE Sondermaschinenbau GmbH was awarded the equalitA seal of approval by the Federal Ministry for Digital and Economic Affairs for its special commitment to supporting women within the company.
This makes HAGE to one of the successful companies that promote women, make this visible and support and promote professional equality for all genders. We are very pleased that values such as equal opportunities, fairness and diversity are practiced within the company and also communicated to the outside world.
The implementation of initiatives such as the 4-day week shows that HAGE is actively committed to the work-life balance of their employees. These measures help to improve the compatibility of career and family, especially for women, who often face the challenge of balancing work and family.
We believe that equal opportunities is not just a buzzword, but a fundamental principle that determines success.
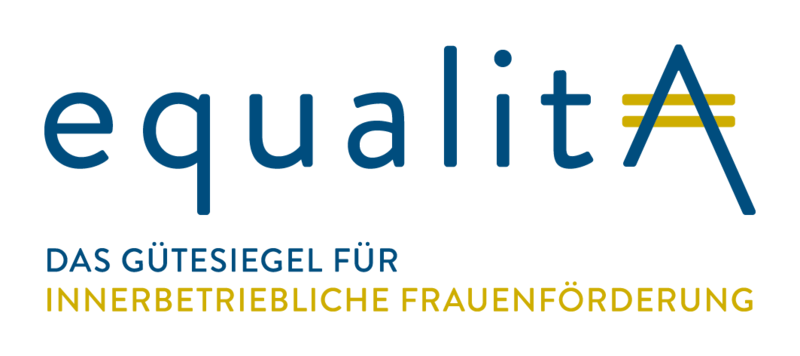
09. Juli 2021
POWERFUL FSW SYSTEM
FOR SIEMENS MOBILITY AUSTRIA GMBH, SIMMERING PLANT
Working in collaboration with Siemens technicians, HAGE has developed a new FSW system for the construction of ultra-modern metro fleets.
In November 2018, Siemens secured a major contract for the refurbishment of one of the world’s oldest metro lines. The new metro trains are set to modernise travel for millions of passengers in one of Europe’s most popular metropolitan areas. In the production of the metro trains, Siemens uses one of the highest-performance friction stir welding systems from HAGE.
With a welding force of 130 kN, the machine is setting new standards in friction stir welding and is one of the most powerful and highest performance FSW systems anywhere in Europe. The wagon components are welded at two stations in shuttle operation using the FSW process. In order to exploit the full welding power of the machine when working with complex components with 3D seam geometries, we use the portal design with six NC axes.
At the heart of the system is the FSW head, developed by HAGE, with integrated force measurement in all axes and the internal V axis. This head permanently monitors and controls the welding process to ensure machine protection.
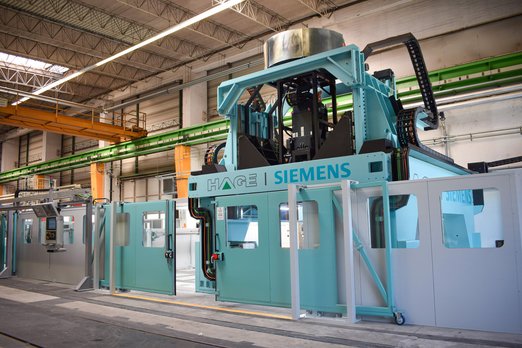
The newly developed, integrated tool changer for split FSW tools is being used for the first time. The tool changer reduces non-productive time and enables efficient automation. In terms of control system, HAGE has opted for the Siemens Sinumerik One for the first time. WeldCheck software, developed by HAGE, monitors the welding process. The software captures and records all process parameters and evaluates the data in real time. The system was handed over to the customer in Vienna in mid-September 2020. At the same time, we expanded the HAGE competence centre to include an identical machine to further advance FSW development.
Development of complex clamping devices including process development
The customer subsequently commissioned joint development of a range of different clamping devices. The project includes:
Preliminary studies to evaluate process forces
Preclamping
Prestressing
Consideration of working spaces and machine restrictions
Well-founded FSW tool and process development through to
Programming of the NC codes based on the welding sequences
Our partner, Siemens Mobility Vienna, is providing active guidance and support through the project planning, thus helping to shorten the integration time from delivery to production. The identical system in Obdach will allow us to start testing and training in advance, and to deliver the initial components. This approach will help to accelerate the development process and guarantees minimum-risk lead times.
A particular highlight is a device to measure and align the component fully automatically after friction stir welding, if required. A Renishaw measuring probe measures the neuralgic points on the workpiece. An algorithm developed by HAGE then calculates the welding force that needs to be applied at the individual points in order to produce a flat component.
10th May 2021
UP TO 500 PROFILE TYPES MACHINED IN FULLY AUTOMATIC OPERATION
At HAGE, every project is a (new) challenge. That was certainly true of the HAGE machining centre for Josko. Employees started development work on the system in February 2019. After many months of work, the customer was able to commission the system in December 2020. Markus Steinkellner (control technology) and Christian Feßl (assembly manager) were heavily involved in construction of the system and give us some first-hand insight into the project.
Fully automatic machining of window profiles in the HAGE machining centre
After manual infeed of the workpieces, a sensor at the end of the infeed conveyor measures the length, width and height of the profiles. The HAGE solution detects the profile type, and then automatically selects the work steps for the next stations. A total of five 4-axis NC feed clamps transport the workpieces through the system.
The first of the two machining centres is fitted with eight spindles. After machining, the profile is moved to the next station, the sawing centre, by a feed clamp. The 5-axis saw makes straight cuts, mitre cuts or shifter cuts depending on the profile. The workpiece is then moved on to the second machining centre, which is fitted with an automatic, 40-way tool changer and where the workpiece is milled, drilled or sawn, depending on the type. A 5-axis machining head performs machining steps on the front. Chips or cuttings are automatically removed and separated by type. The section gripper moves the completed window profiles to the outfeed buffer, from where they are then removed by the system operator.
The fully automatic machining centre unites a range of technologies into a single, overall system. Despite the pool of experience that HAGE employees possess, new challenges are constantly emerging. In this project, control technology was the main focus, as Markus Steinkellner explains: ‘The complex system is equipped with two Sinumerik controls. They might have been commissioned as separate units, but they still need to communicate with one another. The customer created the machining programs in their entirety. We undertook the control, we had never done that before. The measurement sensor technology is also quite extensive – based on the measured data, the system can identify the profile and the machining steps that needed to be completed. We’re currently machining 88 different types. If need be, we can increase that number to 500.’ Christian Feßl sees things in much the same way: ‘The system is extremely complex. So, all the more important that all components are machined or installed with the greatest accuracy. On top of that, we’ve had coronavirus, which has meant constantly adapting to changing regulations.’
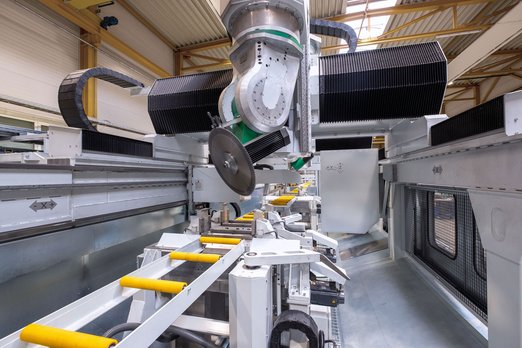
5-axis saw for straight cuts, mitre cuts or shifter cuts
Fact box:
- Surface-protecting workpiece machining
- Up to 500 different profile geometries
- Machine accuracy :±0.1 mm per 3 m
- Axis speeds up to 3 m/s
- Spindle speeds up to 24,000 rpm
- Tool change time BAZ 1 approx. 1 second
- Control: 2x SINUMERIK 840D sL
- 72 servo axes
- 40-way tool changer incl. RFID
- 2-way special tool changer for saw blades up to 650 mm in diameter
- Tool breakage monitoring
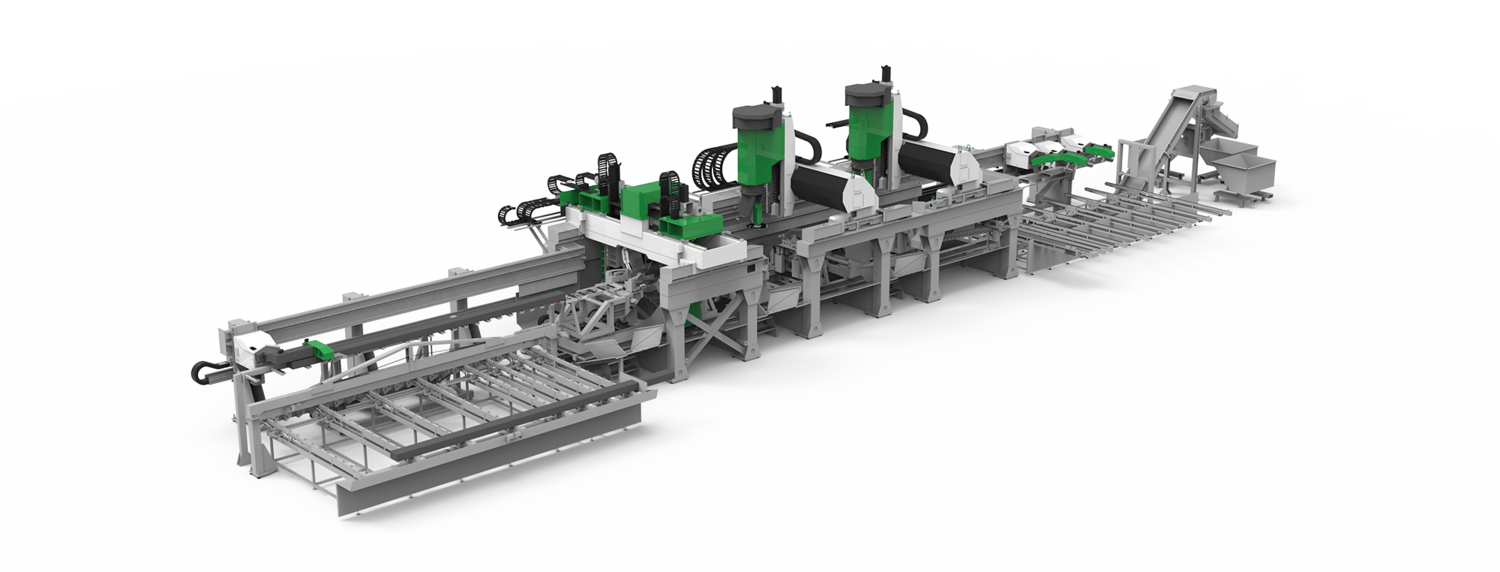
10th April 2020
HAGE and HAGE3D develop a pressure-controlled ventilator
In the fight against the Coronavirus pandemic, HAGE and HAGE3D are developing a pressure-controlled ventilator in close collaboration with the Medical University of Graz.
In Austria, intensive research is currently concentrating on solution approaches to contain the COVID-19 pandemic. As there are regular supply shortages across the world, especially for medical products, the aim of the Austrian initiative is to develop a quickly available, pressure-controlled ventilator for crises or emergency situations.
HAGE and HAGE3D have therefore been working intensively on the development of two prototypes in the last two weeks. HAGE intends to use the innovative spirit and precision of the family company to fight the consequences of the coronavirus. HAGE is already well-known for 5-axis processing centres and friction stir-welding solutions for aerospace and rail technology. The sister company HAGE3D, which, like HAGE, is owned by the Hampel family, has already gathered its first experiences in medical technology through the prototype development of a 3D implant printer.
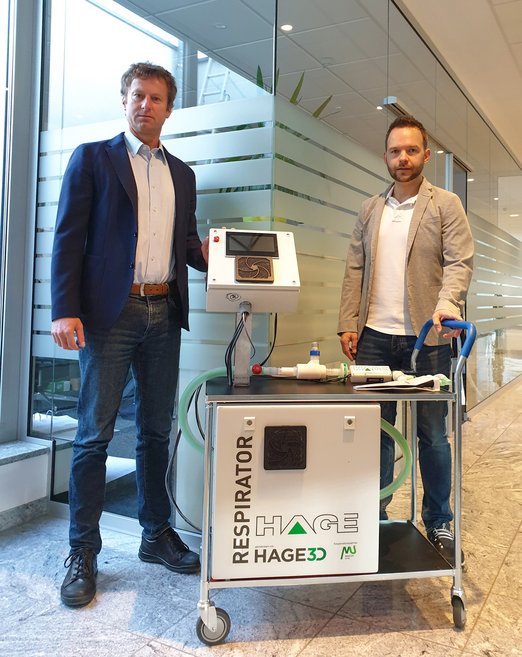
DI Stefan Hampel and DI Peter Freigassner-Sanchez with the ventilator developed by HAGE and HAGE3D
Initial versions based on a bag valve mask and a pneumatic cylinder have been developed, printed and tested by the director DI Peter Freigassner-Sanchez. With the help of the HAGE3D team, a functional, supervised machine was finally created. The requirements and construction were refined across several iterations in close collaboration with experts from the Medical University of Graz. The latest test results – with Prof. Dr. Horst Olschweski, manager of the pulmonology department in Graz – are very promising.
The pressure of the oxygen supply is thereby regulated by a valve system close to the patient in the ventilation tube and controlled by sensors. The transmitted values are displayed graphically on the touch display. A visual and acoustic warning system gives an alert if there is a deviation from the defined ideal values. In order to observe hygiene requirements, many components are made of medical disposable materials and are exchanged or cleaned before each patient. Components that do not come into contact with the patient are cleaned via hygienic surface disinfecting. Functional test series have already been performed.
IV-GF Gernot Pagger recognised the potential importance of the development, and HAGE has been appointed the leader for the development of emergency ventilators within the COVID19 Crisis Task Force of Prof. Ramsauer (TU Graz). The COVID19 Crisis Task Force is in close discussion with Minister Schramböck.
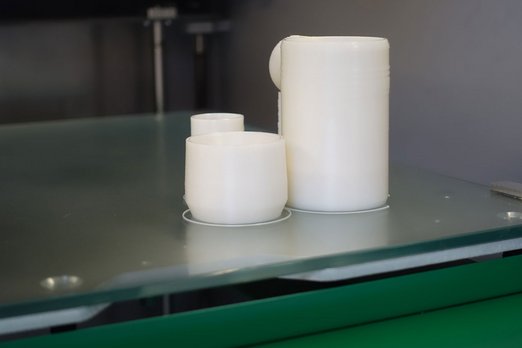
Additively manufactured components for the ventilator with the HAGE3D 3D printer.
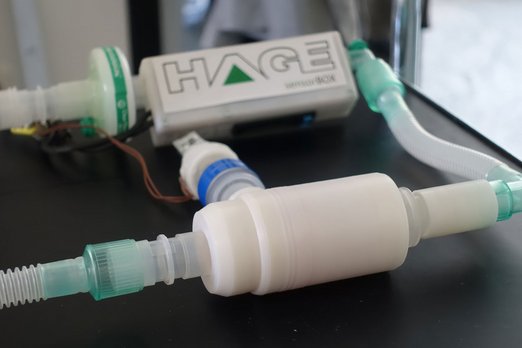
A 3D-printed valve controls the pressure supply of the oxygen.