HAGE Cut sawing machines provide high-precision, automatic sawing of different cross-sections and geometries at variable cutting angles. The sawing function can be combined with deburring and punching. HAGE Cut machines are high-tech, customized saws that can cut the hardest materials.
HAGE Cut saws are designed for full integration into production line concepts with upstream and downstream work steps, such as punching, brush deburring, application of barcodes or parts handling. We developed the HAGE Cut drive system specially in response to the range of process capabilities our customers ask for. Its special geometry gives the saw blade better access to the workpiece; for example it enables cutting of large workpieces using small saw blades. The result is better cut quality and high work rates.
MORE THAN JUST A SAW
Our HSS and hard metal saws achieve high precision thanks to our innovative clamping concepts and highly robust and stable machine design. The machine layout and technical specifications are always customized to suit the customer’s processing needs. The diameter of the clamping flange that holds the saw blade is as large as possible in order to maximize the rigidity of the blade.
- Compatible with any workpiece dimensions
- Thoroughly engineered complete solutions
- User-friendly operation
- Integration with upstream and downstream process steps
- Smart noise protection concept
- Automatic saw blade measurement
- Optimized workpiece handling
- Precise cutting results with HSS and hard metal blades
- Intelligent machine control
Increasing demands on the sawing process requires optimal coordination between machine concept, saw blades and workpieces. Due to our long-standing collaboration with selected partners we can offer you well matched solutions and a lot of positive synergies. The result: highly efficient sawing machines.
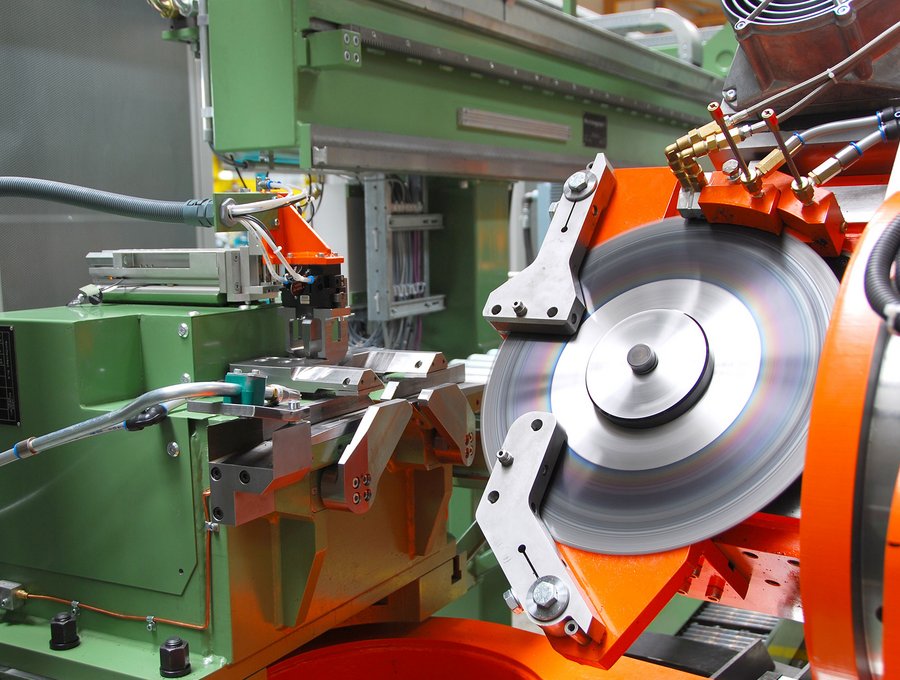
HAGE cut
Sawing lines
We build sawing machines in any required configuration and for all materials and workpiece geometries.
AVAILABLE LINE COMPONENTS:
- Buffer stack with NC feed device
- HM (HSS)-double bevel saw
- HAGE high-performance saw drive
- Transfer handling to deburring station
- NC brush deburring
- Measurement station
- Buffer stack
- Control technology
- Media supplies
- Safety equipment
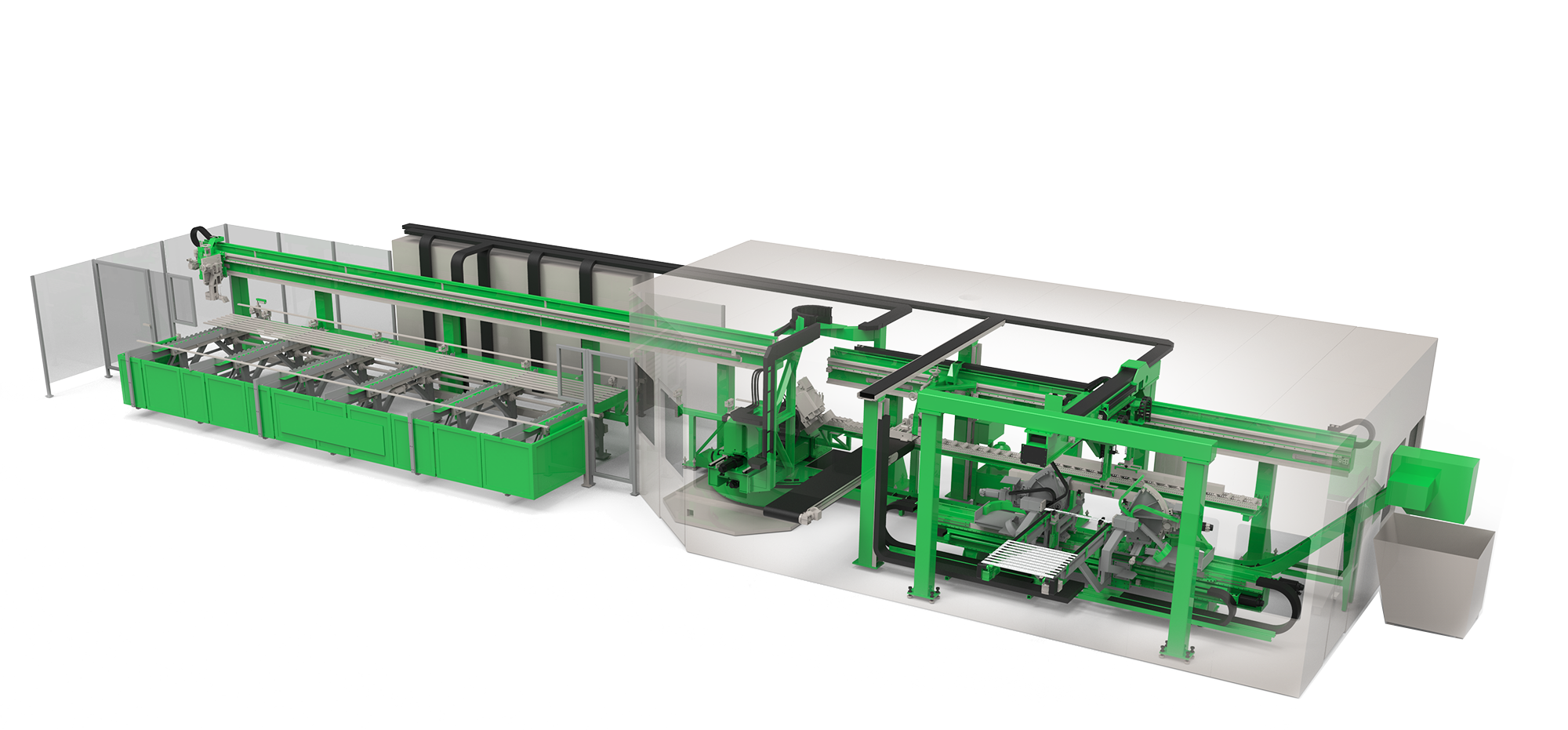
They are available as standalone machines or integrated into production lines. A classic example of a HAGE Cut processing centre is the double bevel saw for profile sections with integrated deburring and measurement.
For fully automated operation, the metal sections are picked from a buffer, checked and passed to an NC feed device. This works together with the NC axes of the double bevel saw to cut the workpieces, which can take the form of a simple end cut or complex cutting of the ends at multiple angles.
The parts are then transported to the NC-adjustable brush deburring station, which can debur all the cut angles the saw can produce, on both ends of each workpiece. After the swarf is blown out of, and off the parts, they are measured, and the finished parts are transported out of the acoustic enclosure to another buffer.
HAGE CUT
Punching lines
HAGE punching lines are highly modular and adaptable. Each machine is specially configured to meet the customer’s requirements.
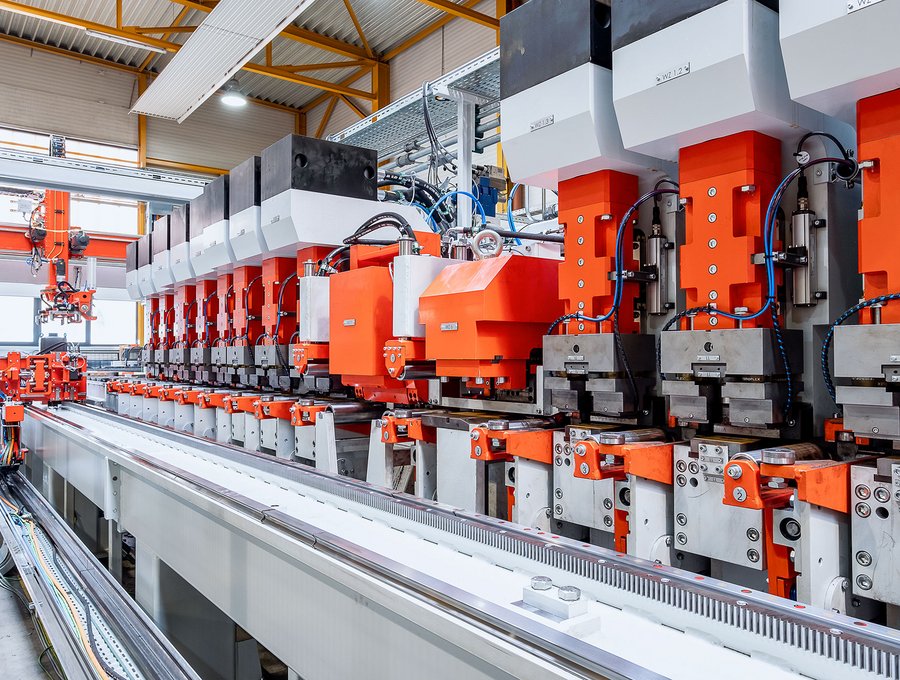
Usually, punching and saw cutting steps are combined in one line, as in the typical cutting and punching lines for steel U sections. This is an innovative automatic processing system for cutting and punching steel U sections of up to 12 m in length, from end to end.
AVAILABLE LINE COMPONENTS:
- Buffers with destacking/separation of parts
- NC sawing station with 2 NC feed grippers
- Waste conveyor for swarf and waste parts from sawing and punching
- Disposal of waste section lengths
- Parts handling
- NC feed grippers
with length measurement function - NC punching tools
- 180° part turner
- Buffer conveyors
- Media supplies: pressurized air,
hydraulic fluid and central lubrication - Control technology
- Safety equipment
The steel sections are transported to the feed conveyor, automatically destacked and if necessary, turned over. Then they are cut to lengths of 720 to 6,000 mm. In subsequent steps, the parts are measured and punched. After a quality check, they are placed on defined buffer conveyors in pairs.
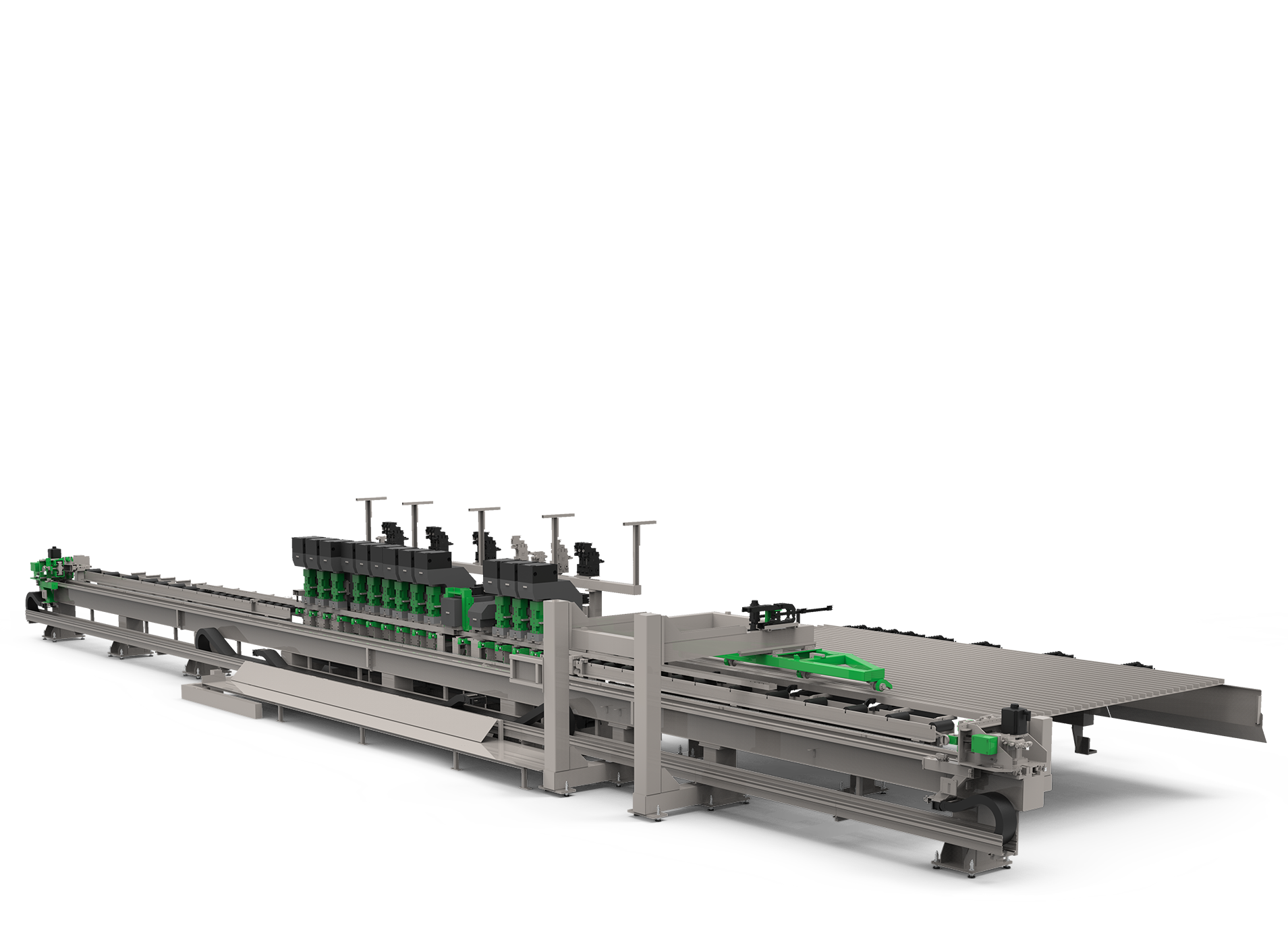