Driven by trends in society such as urbanization and energy efficiency – leading to the need for lightweight construction – the rail industry is faced with new structural challenges. For lightweight construction, aluminium alloys have proven to be an excellent material. Aluminium also becomes relevant for components that are critical for stiffness and crash performance, provided sufficiently high mechanical strength can be achieved while saving weight at the same time; high-performance fabrication methods such as FSW can make this possible. The HAGE FSW processing centres can carry out precision welding of parts up to 80 m long, while HAGE Matic gantry milling machines can work on complete car sidewalls or complete car bodies.
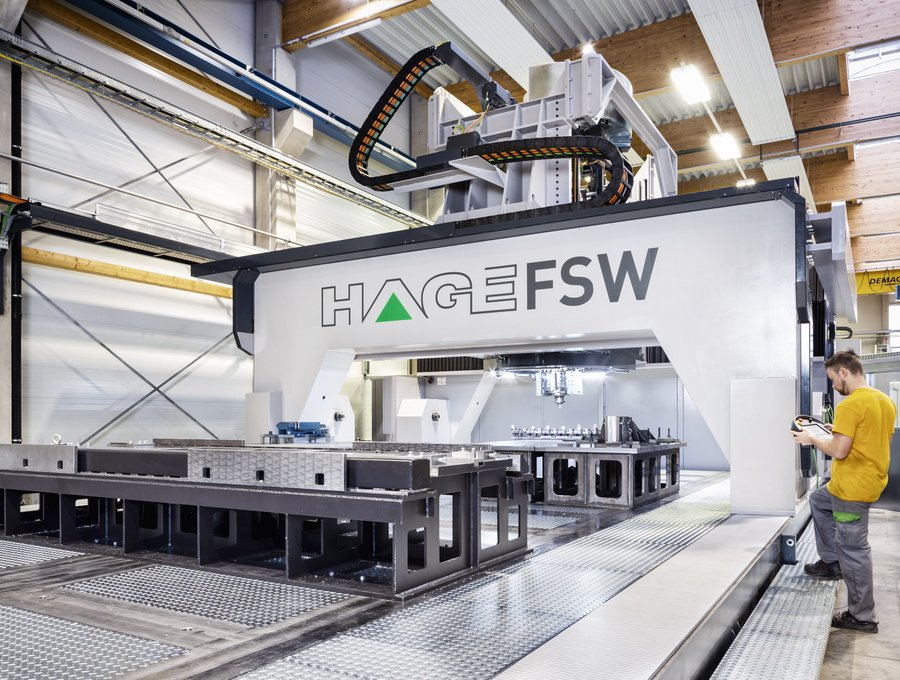
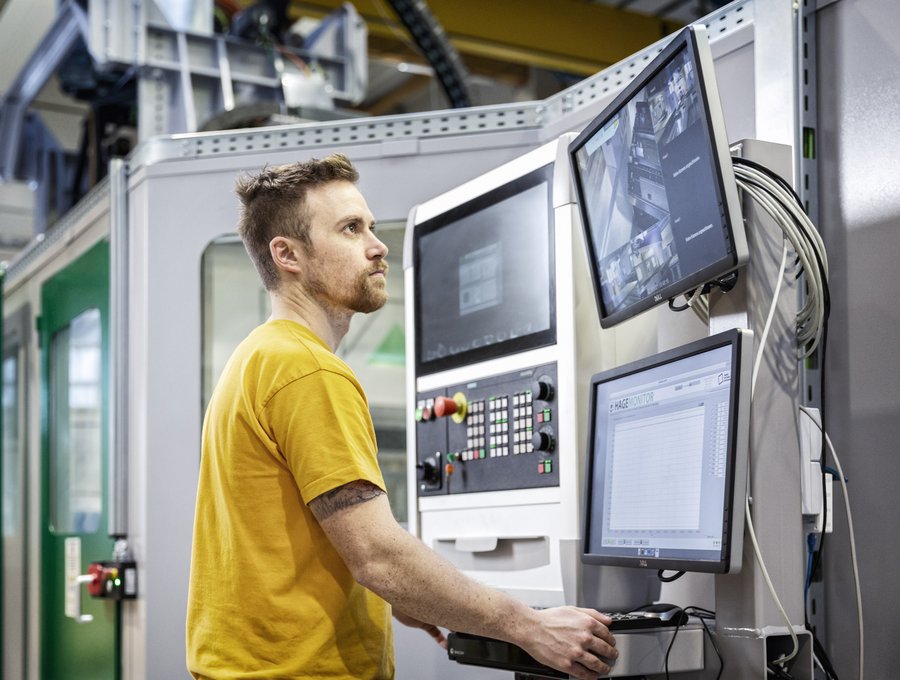
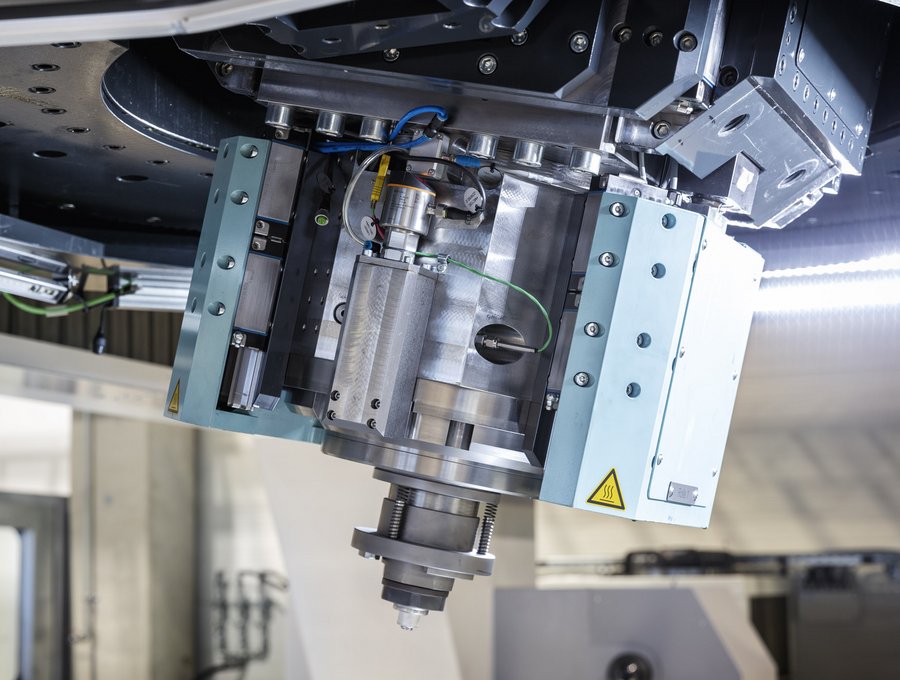
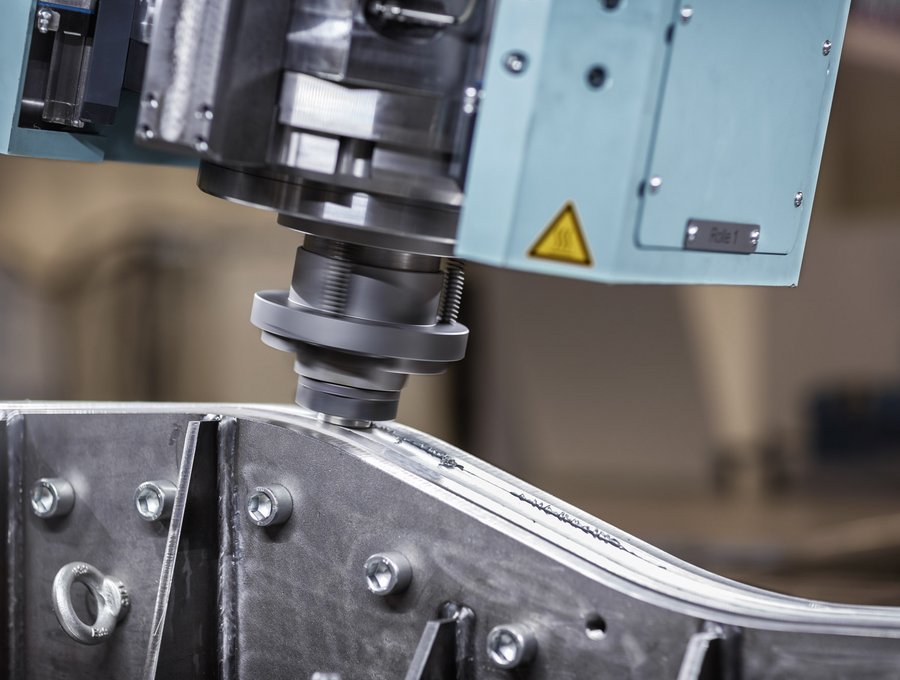
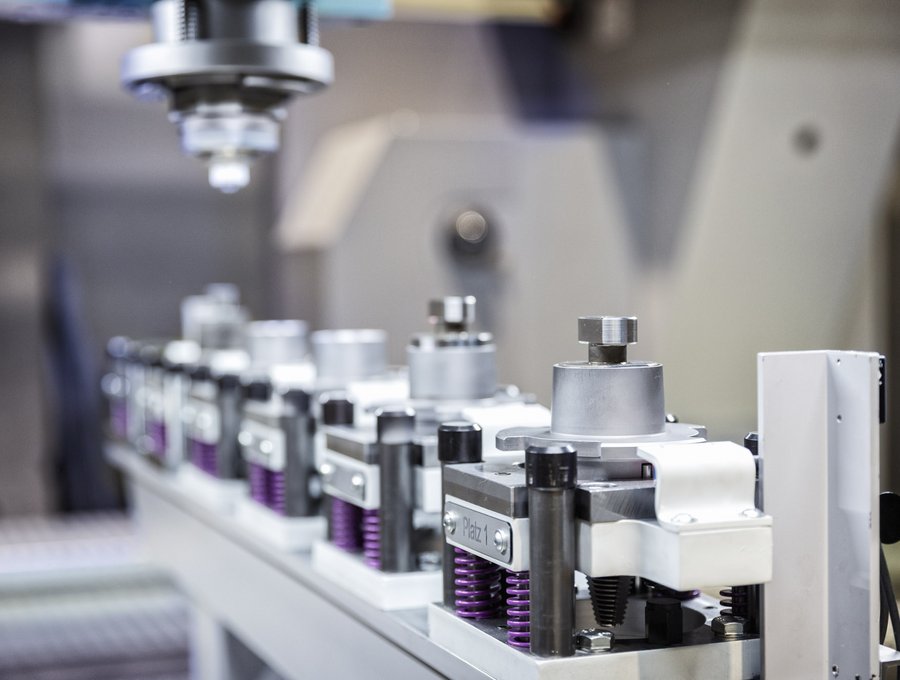
FSW SYSTEM
FOR METRO COMPONENTS
High-performance friction stir welding system with a welding force of 130 kN for the production of metro trains.
The components are welded at two stations in shuttle operation using the FSW process, during which welding forces of up to 130 kN are achieved. At the heart of the system is the newly developed welding head with integrated force measurement in all axes, as well as in the internal V axis. Force measurement enables complete monitoring and control of the welding process as well as machine protection. An additional highlight is the newly developed, integrated tool changer for divided FSW tools, which helps to reduce non-productive time. The new Siemens Sinumerik One is also being used for the first time.
The system is designed not just for the production of metro components – an identical system is also intended to strengthen the HAGE competence centre.
MACHINE HIGHLIGHTS:
- 6-axis FSW machining centre
- 2 stations for shuttle operation
- Machining of 6xxx and 5xxx aluminium alloys
- 3-axis FSW head
- Retractable pin axis
- Automatic tool change for FSW tools
- Range of clamping devices
- HAGE WeldCheck for process monitoring
- FSW process development
- FSW certification
Welding depth: max. 35 mm
Welding force: max. 130 kN
System size: 26 x 10.9 x 4.5 m
Gantry processing centre
for high-speed trains
A total of four HAGE gantry processing centres for high-speed trains were supplied to a customer in Russia.
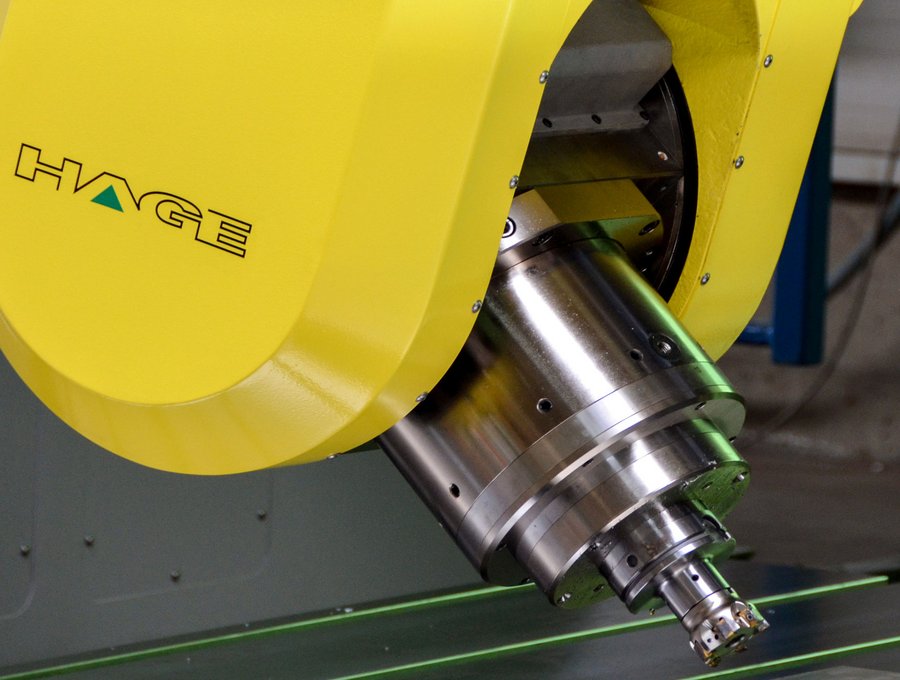
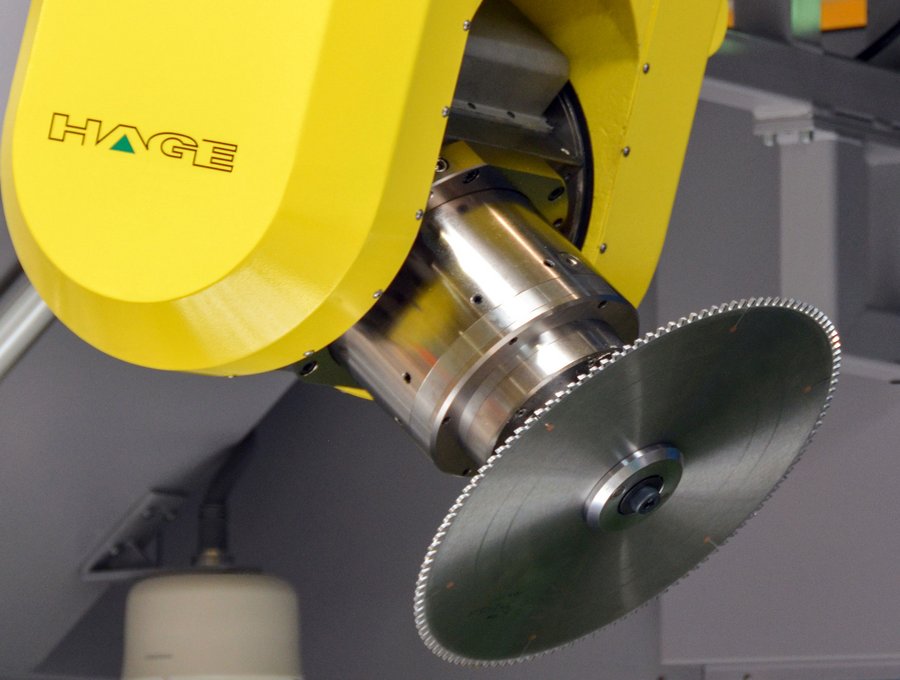
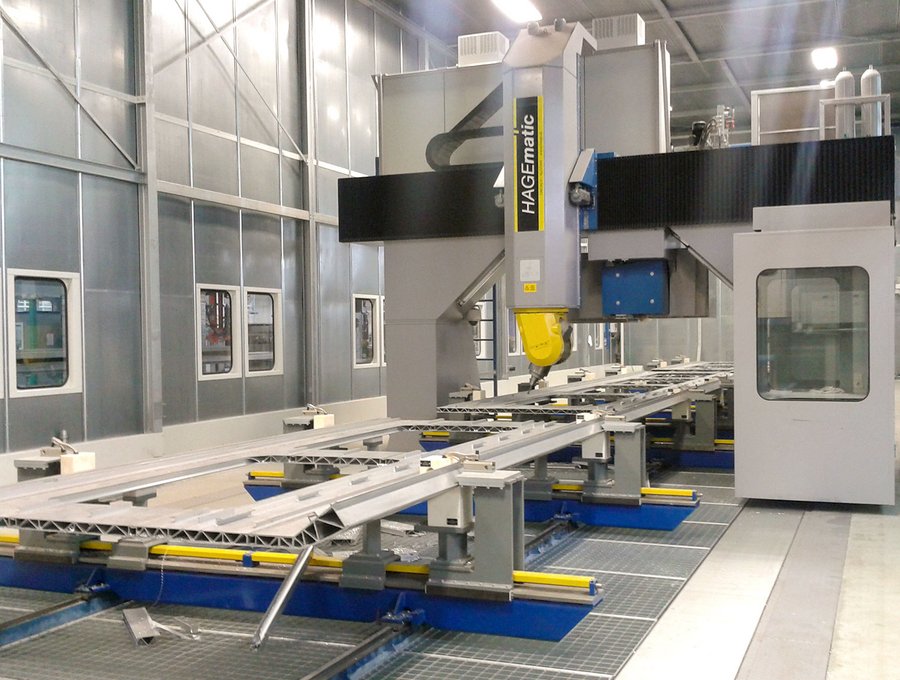
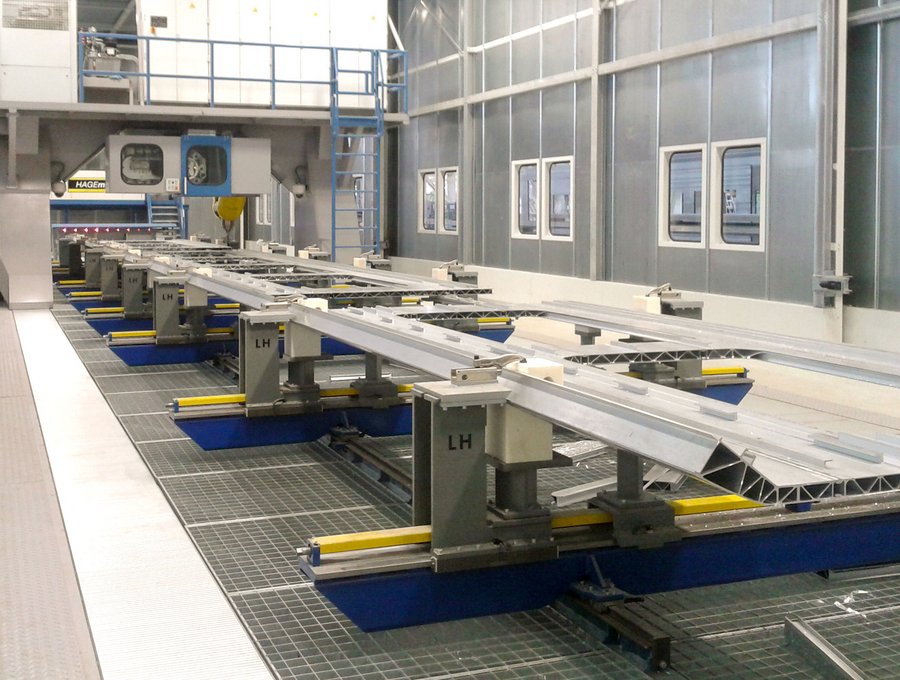
TECHNICAL DATA:
Working envelope
X-axis: 30 m
Y-axis: 5 m
Z-axis: 1.6 m
A-axis: 125° / 95°
C-axis: 450°
Spindle power: 85 kW
Spindle speed: 19.000 rpm
Tool holder: HSK A100
Control: Siemens 840D sl
The large 5-axis gantry milling centres are used to shape bonnets, roof panels, sidewalls, and floor assembies to 0.1-mm tolerances. The parts are subsequently welded together to form high-speed train bodies. The workpieces, which are up to 30 m long, are held in universal clamping systems that were supplied with the machines.